Die cutting method of gauze film layer
A mesh and die-cutting technology, which is applied in metal processing and other directions, can solve the problems of inaccurate manual lamination accuracy, low yield, and difficulty in discharging punching waste, so as to save manual assembly work, ensure lamination accuracy, The effect of increasing productivity
- Summary
- Abstract
- Description
- Claims
- Application Information
AI Technical Summary
Problems solved by technology
Method used
Image
Examples
Embodiment 1
[0034] Such as figure 1 Shown, the die-cutting method of the gauze film layer of the present application comprises the steps:
[0035] Step S10 : Fabricate and form a mesh layer 20 on the upper surface of the material tape 10 , the mesh layer 20 is composed of a plurality of mesh units 21 arranged at intervals.
[0036] Specifically, step S10 is: as Figure 2A As shown, the material tape 10 is used as a carrier medium. After the mesh material is attached to the material tape 10 , the mesh material is punched into a plurality of mesh units 21 by a die-cutting device to form the mesh layer 20 . The shape of the mesh unit 21 may be circular, square, triangular, etc., which is not limited.
[0037] Step S20 : Attach a release film layer 30 on the upper surface of the mesh layer 20 , and the release film layer 30 completely covers the mesh layer 20 .
[0038] Step S30 : Paste an adhesive material on the upper surface of the release film layer 30 , the adhesive material complet...
Embodiment 2
[0049]The die-cutting equipment that present embodiment 2 provides comprises three parts, is sticking device, punching device and stripping device respectively, and sticking device is used for sticking gauze material, release film layer, adhesive material, and punching device is used. For die-cutting the mesh material and the adhesive material, the peeling device is used for peeling off the release film layer. Wherein, after the attaching device attaches the mesh material on the material tape 10, the punching device punches the mesh material to form the mesh layer 20; Attach the release film layer 30 and the adhesive layer 40 in sequence; when the attachment device attaches the adhesive layer 40 to the release film layer 30, the punching device punches the adhesive layer 40, and then the peeling device peels off the release film. Film layer 30 ; after the peeling device peels off the release film layer 30 , the die-cutting device die-cuts the adhesive layer 40 into a plurality...
PUM
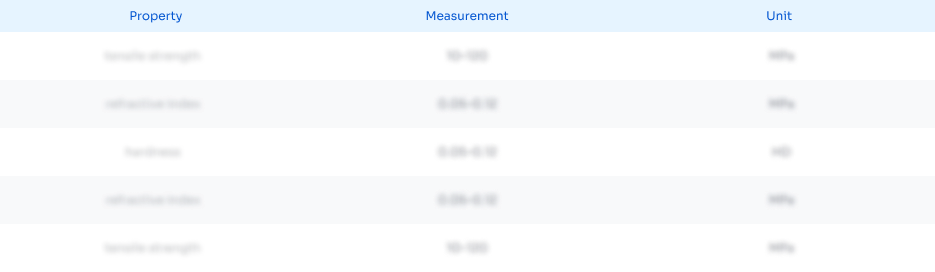
Abstract
Description
Claims
Application Information

- R&D
- Intellectual Property
- Life Sciences
- Materials
- Tech Scout
- Unparalleled Data Quality
- Higher Quality Content
- 60% Fewer Hallucinations
Browse by: Latest US Patents, China's latest patents, Technical Efficacy Thesaurus, Application Domain, Technology Topic, Popular Technical Reports.
© 2025 PatSnap. All rights reserved.Legal|Privacy policy|Modern Slavery Act Transparency Statement|Sitemap|About US| Contact US: help@patsnap.com