Processing method for improving hair effect and water absorption of fabric after resin finishing
A technology of resin finishing and processing method, applied in the field of textile printing and dyeing, can solve the problems of affecting the wearing experience and the decrease of the moisture absorption and breathability of cotton fibers, so as to achieve the effect of improving wool efficiency and wide application.
- Summary
- Abstract
- Description
- Claims
- Application Information
AI Technical Summary
Problems solved by technology
Method used
Examples
Embodiment 1
[0021] Fabric: CM40*CPT40*120*76*60 / 61, organization 1 / 1.
[0022] 1) After singeing-de-boiling-oxygen bleaching-mercerizing-dyeing-liquid ammonia, the fabric is finished without ironing.
[0023] Singeing: Speed: 100m / min, burning, flame intensity: 20mbar.
[0024] Desizing: Desizing enzyme OPT-280 (α-amylase, Shijiazhuang Federal Kete Chemical Co., Ltd.): 3g / L, penetrant WA-M (derivative of polyethylene glycol ether, Zibo Lurui Fine Chemical Co., Ltd. Company): 4g / L, chelating agent SQ-A (phosphate derivative, Zibo Lurui Fine Chemical Co., Ltd.): 2g / L, vehicle speed: 90m / min, steam box 80°C for 15min.
[0025] Scouring: Penetrant WA-M: 4g / L, refining agent SA-U (long-chain fatty alcohol polyoxyethylene ether ester, Zibo Lurui Fine Chemical Co., Ltd.): 4g / L, chelating agent SQ-A: 5mL / kg, caustic soda: 40g / L, vehicle speed: 80m / min, steam box temperature 100℃, piled for 25min.
[0026] Oxygen bleaching: refining agent SA-U: 5g / L, chelating agent SQ-A: 6g / L, hydrogen peroxide stabiliz...
Embodiment 2
[0049] Fabric: CM80 / 2*CM80 / 2*130*90*57 / 58, weave 2 / 1 twill.
[0050] 1) After singeing-de-boiling-oxygen bleaching-mercerizing-dyeing-liquid ammonia, the fabric is finished without ironing. The specific steps are the same as in Example 1.
[0051] 2) Non-ironing process: using modified N-hydroxymethyl dihydroxy ethylene urea resin CR-E: 130g / L, inorganic salt mixture catalyst CT-C: 39g / L, polyethylene fiber protective agent ACN: 20g / L L. Polyurethane resin synergist MNN-7: 10g / L, penetrant MRZ: 3g / L, super-hydrophilic additive QQ-N: 15g / L. Put the prepared material liquid into a rolling tank with a volume of 50L, padding pure cotton fabric, with a rolling margin of 65%, 2 padding 2 rolling, tank liquid level 60%, vehicle speed 60m / min, drying room temperature 100℃ Dry the fabric.
[0052] 3) Then bake: the process is to bake at 150°C for 2.5 min.
[0053] 4) Then carry out washing-softening-preshrinking to the finished product, and the specific steps are the same as in Example 1.
[...
Embodiment 2
[0064] Compared with Comparative Example 2, Example 2 has a higher hair efficiency of 0.6 inches (1.5 cm) in 5 minutes, and has a shorter water absorbency of 33 seconds after washing, and the non-iron performance is equivalent. It fully illustrates that the fabric treated by the process of the present invention has significantly improved wool effect and water absorption, which is better than the traditional non-iron finishing process.
PUM
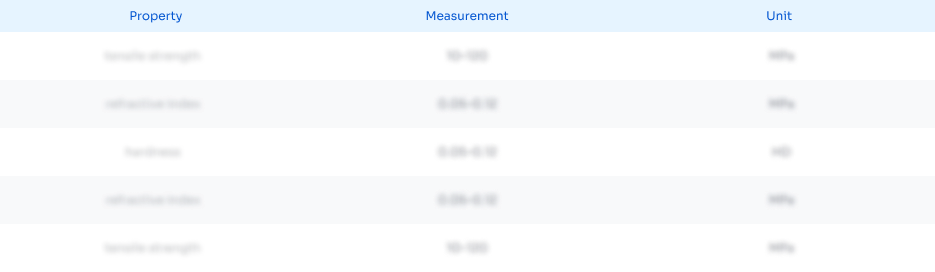
Abstract
Description
Claims
Application Information

- Generate Ideas
- Intellectual Property
- Life Sciences
- Materials
- Tech Scout
- Unparalleled Data Quality
- Higher Quality Content
- 60% Fewer Hallucinations
Browse by: Latest US Patents, China's latest patents, Technical Efficacy Thesaurus, Application Domain, Technology Topic, Popular Technical Reports.
© 2025 PatSnap. All rights reserved.Legal|Privacy policy|Modern Slavery Act Transparency Statement|Sitemap|About US| Contact US: help@patsnap.com