System and method for measuring blade heat exchange coefficient in high-temperature environment
A technology of heat transfer coefficient and high temperature environment, which is applied in the field of measurement system of blade heat transfer coefficient in high temperature environment, and can solve problems such as difficult direct measurement of turbine blades
- Summary
- Abstract
- Description
- Claims
- Application Information
AI Technical Summary
Problems solved by technology
Method used
Image
Examples
Embodiment Construction
[0055] The invention will be further described below in conjunction with the accompanying drawings and specific implementation examples.
[0056] Such as figure 1 As shown, a measurement system for blade heat transfer coefficient in high temperature environment, including blower 1, shut-off valve I2, shut-off valve II11, shut-off valve III13, boiler 3, gas storage tank 4, three-way valve 5, blade to be tested 6, Infrared thermal imager I7, transparent material 8, experimental section 9, air compressor 12, ceramic insulation layer 14, infrared thermal imager II15, thermocouple 17, pressure gauge I16, pressure gauge II10; the air outlet of blower 1 passes through the pipeline and The air inlet of the boiler 3 is connected, the air outlet of the boiler 3 is connected with the inlet of the gas storage tank 4 through a pipeline, the outlet of the gas storage tank 4 is connected with the inlet of one end of the experimental section 9 through a pipeline, and an inlet of the other end...
PUM
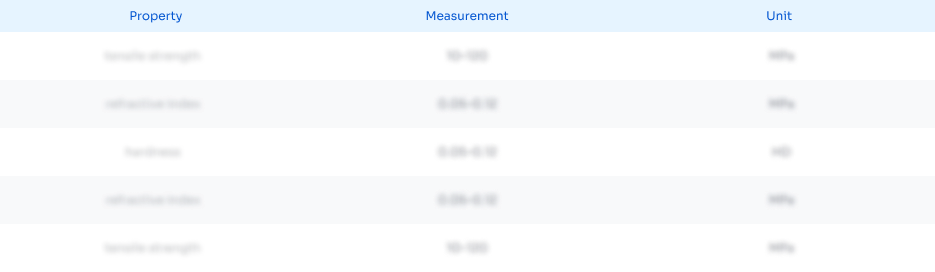
Abstract
Description
Claims
Application Information

- R&D
- Intellectual Property
- Life Sciences
- Materials
- Tech Scout
- Unparalleled Data Quality
- Higher Quality Content
- 60% Fewer Hallucinations
Browse by: Latest US Patents, China's latest patents, Technical Efficacy Thesaurus, Application Domain, Technology Topic, Popular Technical Reports.
© 2025 PatSnap. All rights reserved.Legal|Privacy policy|Modern Slavery Act Transparency Statement|Sitemap|About US| Contact US: help@patsnap.com