Anti-detonation ceramic kiln
A kiln and pottery technology, applied in the field of ceramic molding equipment, can solve problems such as explosion, fire, and restricting the use of kilns
- Summary
- Abstract
- Description
- Claims
- Application Information
AI Technical Summary
Problems solved by technology
Method used
Image
Examples
Embodiment 1
[0030] Such as Figure 1-Figure 5 As shown, the present invention provides a deflagration-proof pottery kiln, comprising a kiln frame 1 and kiln bricks 2 arranged in the kiln frame 1, the upper end of the kiln frame 1 is hingedly provided with a top cover 3, the top The cover 3 can play the role of sealing the heat dissipation vent 5 during the firing process of ceramics, so as to prevent energy loss caused by heat transfer to the outside world;
[0031] The kiln bricks 2 are all provided with a mortise and tenon structure 21, and the adjacent kiln bricks 2 are spliced through the mortise and tenon structure 21. On the one hand, the mortise and tenon structure 21 has the effect of quickly installing the kiln brick 2, and on the other hand, it is an exquisite component The connection method enables the kiln brick 2 to offset a certain internal pressure of the kiln brick 2 through deformation under the high temperature load of high temperature expansion and contraction, and re...
Embodiment 2
[0041] Such as Figure 1-Figure 5 As shown, this embodiment is a further optimization made on the basis of Embodiment 1. Specifically, the lower end of the kiln frame 1 is provided with a fixed shaft 13, and the lower end of the fixed shaft 13 is provided with a pulley 14. Brake pads are arranged on the pulley 14 .
[0042] In this embodiment, a fixed shaft 13 and a pulley 14 are arranged at the lower end of the kiln frame 1 to facilitate the movement and maintenance of the kiln frame 1 as a whole, and brake pads are set on the pulley 14 to prevent the kiln frame 1 from moving during operation, causing problems with the kiln frame 1. Collision with other equipment or staff, resulting in loss.
Embodiment 3
[0044] Such as Figure 1-Figure 5 As shown, this embodiment is a further optimization made on the basis of Embodiment 2. Specifically, in order to facilitate the opening and closing of the top cover 3 and the box door 15, the top cover 3 and the box door 15 are provided with handles 17, the handles 17 are provided with anti-slip lines, anti-slip lines are convenient to increase the hand friction between the operator and the handle 17 to prevent slipping.
[0045] working principle
[0046] The present invention is a deflagration-proof pottery kiln, the distribution of each part is as follows: Figure 1-Figure 5 As shown, when in use, due to the mortise and tenon structure 21 used between the kiln bricks 2, the mortise and tenon structure 21 has the effect of quickly installing the kiln bricks 2 on the one hand, and on the other hand, the exquisite component connection method makes the kiln bricks 2 hot under high temperature. Under the high-temperature load of expansion and ...
PUM
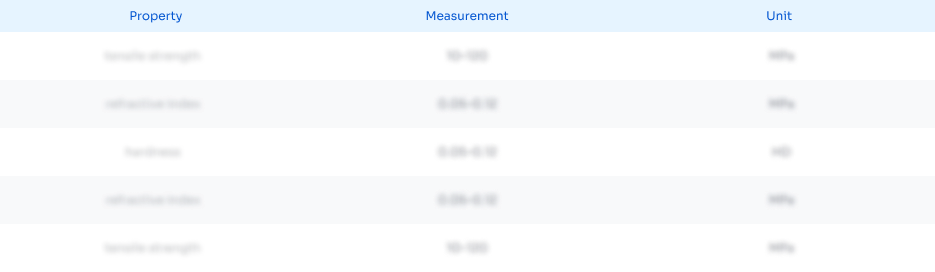
Abstract
Description
Claims
Application Information

- Generate Ideas
- Intellectual Property
- Life Sciences
- Materials
- Tech Scout
- Unparalleled Data Quality
- Higher Quality Content
- 60% Fewer Hallucinations
Browse by: Latest US Patents, China's latest patents, Technical Efficacy Thesaurus, Application Domain, Technology Topic, Popular Technical Reports.
© 2025 PatSnap. All rights reserved.Legal|Privacy policy|Modern Slavery Act Transparency Statement|Sitemap|About US| Contact US: help@patsnap.com