Safety control system and method for drill jambo power unit
A power unit, safety control technology, applied in the control system, motor speed or torque control, motor control and other directions, can solve the problems of motor damage, reduce the service life of the motor and power grid, etc., to achieve small inrush current and improve life , the effect of reducing costs
- Summary
- Abstract
- Description
- Claims
- Application Information
AI Technical Summary
Problems solved by technology
Method used
Image
Examples
Embodiment 1
[0066] In this embodiment, the motor unit includes a main motor 81, the incoming line end of the main motor 81 is connected with the outgoing line end of the switching contactor 403 and the outgoing line end of the bypass contactor 405, the main electric machine 81 is provided with a first motor monitoring unit, the second A motor monitoring unit includes: a first speed sensor 811 , a first coupling temperature sensor 812 , a first stator winding temperature sensor 813 , and a first rotor winding sensor 814 .
[0067]Wherein the first rotational speed sensor 811 is connected with MCU 5 through the signal line, is used for detecting main motor speed, and sends to MCU; The first joint temperature sensor 812 is connected with MCU 5 through signal line, is used for detecting main motor coupling The temperature of the coupling is sent to the MCU 5; the first coupling temperature sensor 812 is connected to the MCU 5 through a signal line for detecting the temperature of the motor cou...
Embodiment 2
[0069] In this embodiment, the motor unit includes a water pump motor 82, the inlet end of the water pump motor 82 is connected to the outlet end of the switching contactor 403 and the outlet end of the bypass contactor 405, and the first motor monitoring unit is arranged in the water pump motor 82, Corresponding sensors are arranged on corresponding components of the water pump motor 82 for monitoring whether the water pump motor 82 is abnormal.
Embodiment 3
[0071] In this embodiment, the motor unit includes a main motor 81 and a water pump motor 82. The main motor 81 is provided with a first motor monitoring unit, and the water pump motor 82 is provided with a second motor monitoring unit. The first motor monitoring unit includes: a first rotating speed Sensor 811 , first coupling temperature sensor 812 , first stator winding temperature sensor 813 , first rotor winding sensor 814 . Wherein the first rotational speed sensor 811 is connected with MCU 5 through the signal line, is used for detecting main motor speed, and sends to MCU5; The first coupling temperature sensor 812 is connected with MCU 5 through signal line, is used for detecting main motor shaft coupling The temperature of the coupling is sent to the MCU 5; the first coupling temperature sensor 812 is connected to the MCU 5 through a signal line to detect the temperature of the main motor coupling and is sent to the MCU 5; the first stator winding temperature sensor 81...
PUM
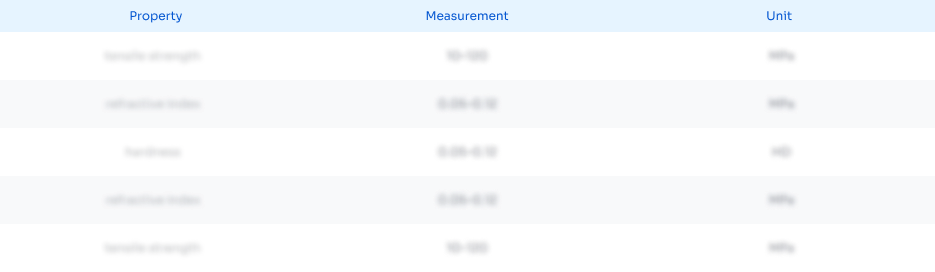
Abstract
Description
Claims
Application Information

- R&D Engineer
- R&D Manager
- IP Professional
- Industry Leading Data Capabilities
- Powerful AI technology
- Patent DNA Extraction
Browse by: Latest US Patents, China's latest patents, Technical Efficacy Thesaurus, Application Domain, Technology Topic, Popular Technical Reports.
© 2024 PatSnap. All rights reserved.Legal|Privacy policy|Modern Slavery Act Transparency Statement|Sitemap|About US| Contact US: help@patsnap.com