Oil-lubricated kinematic module connecting system, mainly the transmission or bearing modules of industrial robot; method of kinematic module lubrication
A technology for industrial robots and motion modules, applied in manipulators, manufacturing tools, etc., can solve the problems of not restricting the freedom of robot motion, reducing dynamic characteristics, unsuitable for robot transmission or bearing modules, etc., to reduce environmental burden, increase life and Reliability and lubricity improvement effect
- Summary
- Abstract
- Description
- Claims
- Application Information
AI Technical Summary
Problems solved by technology
Method used
Image
Examples
example 1
[0045] In this example and based on figure 1 , the manipulator has four revolving joints mounted and moved through a motion module 1 in the form of a bearing reducer. Three of these motion modules 1 , considered the most dynamically utilized, cooperate with gearboxes through pipe and hose connections. The oil circulation between the movement modules 1 is provided by the movement of the planetary gears of the reducer itself; there is no need to connect the pump 3 .
example 2
[0047] In this example, based on figure 2 , the oil-filled interconnection of all six motion modules 1 of the industrial robot. The connection is a simple series circulation loop where the oil flows from the highest motion module 1 to the next motion module 1 . From the last lowest movement module 1 , the oil is pumped to the highest movement module 1 via the suction filter 12 and via the filter device 4 by the pump 3 . To protect the pump 3 and its motor, the system is equipped with a bypass valve and two pressure sensors connected before and after the pump 3 .
[0048] The box of the lowest motion module 1 is used as the oil box for the whole system. The motion module is designed for maximum static and dynamic loads as it carries all adjacent arms and joints.
example 3
[0050] In this example, according to image 3 , the series connection of the previous example is supplemented by a separate filter circuit comprising an oil tank 9 into which oil flows from the last movement module 1 . A pressure variation compensator 14 is connected to the oil reservoir 9 ; this compensator is in the form of a breather filter in this example. The oil reservoir 9 is connected via the pump 3 to the branch circuit with the movement module 1; it is also connected to the filter device circuit 4, which consists of a replaceable filter element 8, the pump 3 with the motor, the bypass valve and a pair of pressure sensors . The suction filter 12 serves as protection against the introduction of coarse impurities into the pump 3 .
PUM
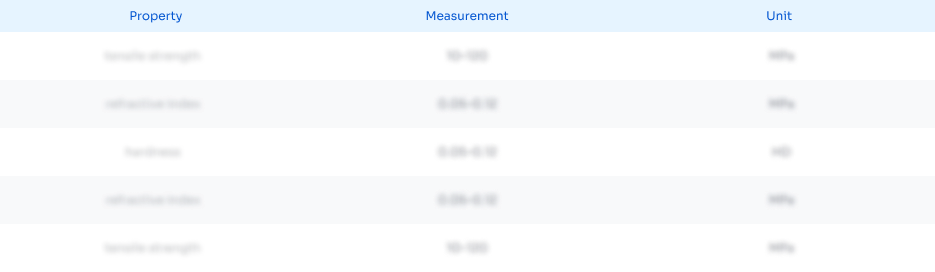
Abstract
Description
Claims
Application Information

- Generate Ideas
- Intellectual Property
- Life Sciences
- Materials
- Tech Scout
- Unparalleled Data Quality
- Higher Quality Content
- 60% Fewer Hallucinations
Browse by: Latest US Patents, China's latest patents, Technical Efficacy Thesaurus, Application Domain, Technology Topic, Popular Technical Reports.
© 2025 PatSnap. All rights reserved.Legal|Privacy policy|Modern Slavery Act Transparency Statement|Sitemap|About US| Contact US: help@patsnap.com