Logical support structures and anti-collision devices for offshore structures
A technology of anti-collision devices and offshore structures, which is applied in the field of marine and ships, can solve the problems of metal foam plastic damage, low rigidity, deformation damage, etc., and achieve the effect of reducing the contact force of impact
- Summary
- Abstract
- Description
- Claims
- Application Information
AI Technical Summary
Problems solved by technology
Method used
Image
Examples
Embodiment 1
[0042] see figure 2 , the present application is a logical support structure for offshore structures, including a bearing part 1, a fixing part 3, a brace 2 and a linear spring 4; the bearing part 1 and the fixing part 3 are arranged in parallel; the brace 2 includes a first The diagonal brace 21 and the second diagonal brace 22, the first diagonal brace 21 and the second diagonal brace 22 are all arranged in pairs, and one end of the two first diagonal braces 21 is respectively hinged at the two ends of the bearing part, and the other end faces the opposite direction. The direction is inclined, and one end of the two second diagonal braces 22 is respectively hinged on the two ends of the fixed portion, and the other end is inclined in the opposite direction, and the other end is respectively hinged with the other end of the corresponding first diagonal brace; the linear The spring 4 is arranged between the bearing part and the fixing part, and its two ends are respectively h...
Embodiment 2
[0048] see Figure 6 and Figure 7 , further, the present application also provides an anti-collision device 6 for offshore structures, including a load-bearing part 1, a fixed part 3 and a spring system, the load-bearing part 1 and the fixed part 3 are arranged in parallel, and the spring system includes multiple sets of consecutively arranged spring unit, each spring unit includes a brace 2 and a linear spring 4, the brace 2 includes a first brace 21 and a second brace 22, the first brace 21 and the second brace 22 are formed For the setting, one end of the two first diagonal braces 21 is hinged on the bearing part 1 at intervals, and the other end is inclined in the opposite direction, and one end of the two second diagonal braces 22 is hinged on the fixed part at intervals, and the other end faces the opposite direction. The direction is inclined, the other end of which is respectively hinged with the other end of the corresponding first diagonal brace 21; The intersecti...
Embodiment 3
[0089] see Figure 8 ~ Figure 10 , the present application also provides an anti-collision structure for offshore wind turbines, including the wind turbine and an anti-collision device 6, the anti-collision device 6 adopts the logical anti-collision device described in Embodiment 2, the anti-collision device is vertically arranged, and its The fixing part is fixed on the outer periphery of the wind turbine tower 7 .
[0090] Specifically, the anti-collision device is vertically arranged at the position where the wind turbine tower 7 is close to the sea surface, and acts on the bearing part 1 of the anti-collision device when the ship 8 docks or collides normally.
PUM
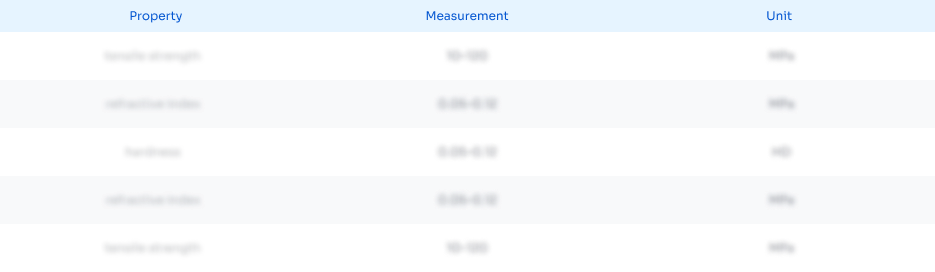
Abstract
Description
Claims
Application Information

- Generate Ideas
- Intellectual Property
- Life Sciences
- Materials
- Tech Scout
- Unparalleled Data Quality
- Higher Quality Content
- 60% Fewer Hallucinations
Browse by: Latest US Patents, China's latest patents, Technical Efficacy Thesaurus, Application Domain, Technology Topic, Popular Technical Reports.
© 2025 PatSnap. All rights reserved.Legal|Privacy policy|Modern Slavery Act Transparency Statement|Sitemap|About US| Contact US: help@patsnap.com