Self-moving die punching machine
A stamping machine and self-moving technology, which is applied in the field of stamping machines, can solve the problems of low drilling efficiency, time-consuming and labor-consuming, and achieve the effect of improving the drilling efficiency
- Summary
- Abstract
- Description
- Claims
- Application Information
AI Technical Summary
Problems solved by technology
Method used
Image
Examples
Embodiment 1
[0030] A self-moving die stamping machine, such as figure 1 As shown, it includes a base 1, a bracket 2, a moving mechanism 3 and a punching mechanism 4, a bracket 2 is installed on the front side of the right part of the base 1, a moving mechanism 3 is arranged on the base 1, and a punching mechanism 4 is arranged on the base 1. The punching mechanism 4 is connected with the movement mechanism 3 .
[0031] When the composite slatted board needs to be stamped and punched, the composite slatted board is manually placed in the parts of the movement mechanism 3, so that the position of the last row of composite slatted boards to be punched is directly below the parts of the punching mechanism 4 , and then start the parts of the moving mechanism 3, and the parts of the moving mechanism 3 will drive the composite slatted plate to move back intermittently. At the same time, the parts in the punching mechanism 4 will reciprocate up and down. When the composite slatted plate stops mov...
Embodiment 2
[0033] In particular, as Figure 2-3 As shown, the motion mechanism 3 includes a motor 31, a first pulley 32, a first flat belt 33, a first rotating shaft 34, a second rotating shaft 35, a half-moon disc 36, a first driving lever 37, a third rotating shaft 38, a hexagonal Disc 39, steering gear 310, first gear 311, fourth rotating shaft 312, fifth rotating shaft 313, second gear 314, rack 315, bearing frame 316 and first slide rail 317, base 1 middle part front side is installed with Motor 31, the output shaft of motor 31 is connected with the first rotating shaft 34, and the left rear side of support 2 top is rotated and is provided with the second rotating shaft 35, and the front side of the second rotating shaft 35 and the middle part of the first rotating shaft 34 are all provided with the first belt pulley 32 A first flat belt 33 is wound between the two first pulleys 32, a half-moon disc 36 is installed on the rear side of the second rotating shaft 35, and a first lever ...
Embodiment 3
[0036] according to figure 2 and Figure 4As shown in the diagram, the punching mechanism 4 includes a second pulley 41, a second flat belt 42, a sixth rotating shaft 43, a pressing turntable 44, a second driving lever 45, a spring 46, a push plate 47, a punching rod 48 and The second slide rail 49, the front side of the middle part of the base 1 is rotatably provided with a sixth rotating shaft 43, the sixth rotating shaft 43 front side and the first rotating shaft 34 rear side are equipped with a second pulley 41, and the two second pulleys 41 pass through the second The flat belt 42 is connected, the sixth rotating shaft 43 rear end is equipped with a pressing turntable 44, the pressing rotating disc 44 top is provided with a second shift lever 45, the rear side of the base 1 is provided with a second slide rail 49, the sixth rotating shaft 43 rear end and The front side of the upper part of the second slide rail 49 is rotationally connected, and a push plate 47 is slidin...
PUM
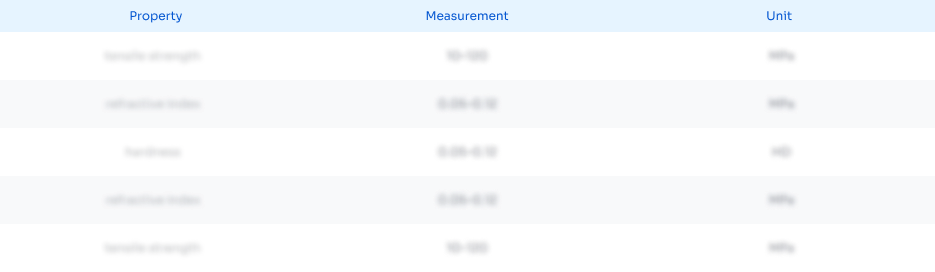
Abstract
Description
Claims
Application Information

- Generate Ideas
- Intellectual Property
- Life Sciences
- Materials
- Tech Scout
- Unparalleled Data Quality
- Higher Quality Content
- 60% Fewer Hallucinations
Browse by: Latest US Patents, China's latest patents, Technical Efficacy Thesaurus, Application Domain, Technology Topic, Popular Technical Reports.
© 2025 PatSnap. All rights reserved.Legal|Privacy policy|Modern Slavery Act Transparency Statement|Sitemap|About US| Contact US: help@patsnap.com