The method of cleaning the blast furnace before shutting down
A blast furnace and furnace washing technology, which is applied to the field of blast furnace iron-making empty material line shutdown, can solve the problem of unclean furnace walls, prolonged blast furnace shutdown time, and long processing time of furnace wall adhesions and hearth deposits, etc. problems, to achieve the effect of saving blast furnace shutdown time, improving fluidity, and shortening cleaning time
- Summary
- Abstract
- Description
- Claims
- Application Information
AI Technical Summary
Problems solved by technology
Method used
Image
Examples
Embodiment 1
[0047] A method for cleaning a blast furnace before shutdown, comprising:
[0048] S1. Use silica, medium marble and manganese ore as auxiliary materials, and distribute them in the throat of the blast furnace.
[0049] S2. Under the condition of the edge temperature of 275°C, smelting by washing furnace for 5 days: first smelting according to the coal injection ratio of 160kg / t for 3 days; then smelting according to the coal injection ratio of 110kg / t for 1.5 days; then gradually reducing the coal injection ratio , and started full-coke smelting on the 4.67th day.
[0050] S3. Add wind-off material to carry out pre-shut-off operation.
[0051] In this example, the model of blast furnace is 1050m 3 Level, the cloth operation to achieve the edge temperature requirement is as follows:
[0052] Adjust the cloth matrix from the cloth method in Table 1 to the cloth method in Table 2. Among them, the cloth for the outer ring of ore is reduced from 3 rings to 2 rings, the cloth f...
Embodiment 2
[0058] A method for cleaning a blast furnace before shutdown, comprising:
[0059] S1. Use silica, medium marble and manganese ore as auxiliary materials, and distribute them in the throat of the blast furnace.
[0060] S2. Under the condition of edge temperature of 250°C, furnace washing and smelting for 5 days: first smelting at a coal injection ratio of 155kg / t for 3 days; then smelting at a coal injection ratio of 100kg / t for 1.3 days; then gradually reducing the coal injection ratio , and started full-coke smelting on the 4.67th day.
[0061] S3. Add wind-off material to carry out pre-shut-off operation.
[0062] Wherein, the component content in the molten iron and the temperature of the molten iron are the same as in Example 1, and the component content in the slag is the same as in Example 1.
Embodiment 3
[0064] A method for cleaning a blast furnace before shutdown, comprising:
[0065] S1. Use silica, medium marble and manganese ore as auxiliary materials, and distribute them in the throat of the blast furnace.
[0066] S2. Under the condition of edge temperature of 300°C, smelting by washing the furnace for 5 days: first smelting according to the coal injection ratio of 165kg / t for 3 days; then smelting according to the coal injection ratio of 120kg / t for 1.7 days; then gradually reducing the coal injection ratio , and started full-coke smelting on the 4.67th day.
[0067] S3. Add wind-off material to carry out pre-shut-off operation.
[0068] Wherein, the component content in the molten iron and the temperature of the molten iron are the same as in Example 1, and the component content in the slag is the same as in Example 1.
PUM
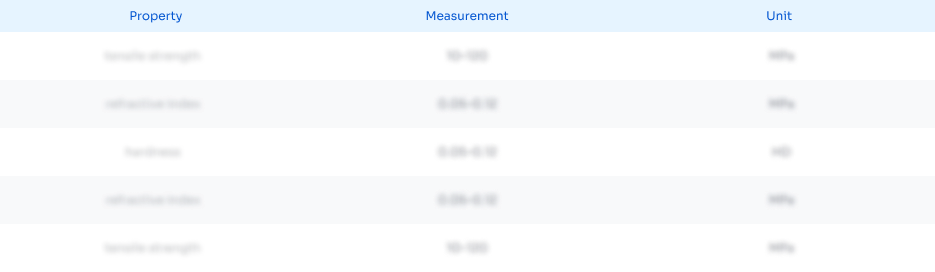
Abstract
Description
Claims
Application Information

- R&D
- Intellectual Property
- Life Sciences
- Materials
- Tech Scout
- Unparalleled Data Quality
- Higher Quality Content
- 60% Fewer Hallucinations
Browse by: Latest US Patents, China's latest patents, Technical Efficacy Thesaurus, Application Domain, Technology Topic, Popular Technical Reports.
© 2025 PatSnap. All rights reserved.Legal|Privacy policy|Modern Slavery Act Transparency Statement|Sitemap|About US| Contact US: help@patsnap.com