Fatigue life prediction method and device based on weighted average maximum shear stress plane
A technology of fatigue life prediction and shear stress, which is used in measuring devices, using stable shear force to test the strength of materials, and testing of mechanical parts, etc. Effect
- Summary
- Abstract
- Description
- Claims
- Application Information
AI Technical Summary
Problems solved by technology
Method used
Image
Examples
Embodiment Construction
[0066] Embodiments of the high cycle multiaxial fatigue life prediction method based on the weighted average maximum shear stress plane according to the present invention will be described below with reference to the accompanying drawings. Those skilled in the art would recognize that the described embodiments can be modified in various ways or combinations thereof without departing from the spirit and scope of the invention. Accordingly, the drawings and description are illustrative in nature and not intended to limit the scope of the claims. Also, in this specification, the drawings are not drawn to scale, and like reference numerals denote like parts.
[0067] The high-cycle multiaxial fatigue life prediction method based on the weighted average maximum shear stress plane includes the following steps:
[0068] Step 1): Obtain the load history of the notched parts, such as Figure 2a Shown, F N is the loaded axial force, M T For loading to torque, the load history of the...
PUM
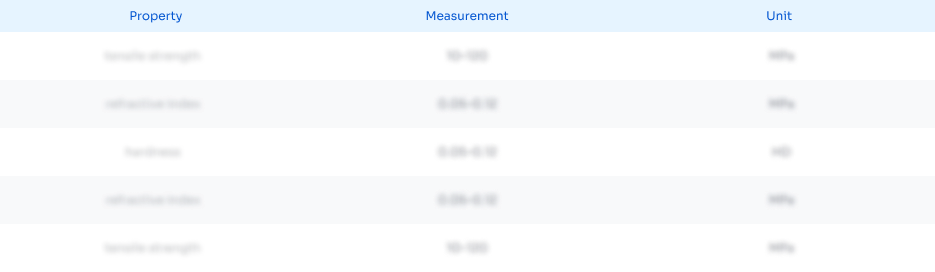
Abstract
Description
Claims
Application Information

- R&D
- Intellectual Property
- Life Sciences
- Materials
- Tech Scout
- Unparalleled Data Quality
- Higher Quality Content
- 60% Fewer Hallucinations
Browse by: Latest US Patents, China's latest patents, Technical Efficacy Thesaurus, Application Domain, Technology Topic, Popular Technical Reports.
© 2025 PatSnap. All rights reserved.Legal|Privacy policy|Modern Slavery Act Transparency Statement|Sitemap|About US| Contact US: help@patsnap.com