Gap calibration method for paired heating rollers of composite material
A composite material and heating roller technology, applied in the field of carbon fiber manufacturing, can solve the problems of large measurement error, influence of operation experience, dangerous operation, etc., to achieve the effect of small measurement error, safe operation, and elimination of interference
- Summary
- Abstract
- Description
- Claims
- Application Information
AI Technical Summary
Problems solved by technology
Method used
Image
Examples
Embodiment 1
[0017] Embodiment one: its concrete steps are:
[0018] Steps to calibrate the gap of the displacement sensor for the first time:
[0019] 1. By using a mechanical feeler gauge for simple calibration, adjust the gap between the two ends of the pair of heating rollers to a value close to 2mm.
[0020] 2. Start the pair of heating rollers to make them rotate at a low speed in the normal working direction.
[0021] 3. Put two pieces of pure lead wire with a diameter of 6 mm into the two ends of the heating roller surface 2 (working area) at the same time, let the lead wire rotate with the heating roller (do not drag the lead wire to prevent the lead wire from breaking), and the lead wire is placed between the pair of heating rollers. Plastic deformation occurs under the extrusion of the roller surface 2, and when the lead wire follows and rotates for a certain distance, the heating roller is reversed to make the lead wire back out.
[0022] 4. At this time, the lead wire has be...
Embodiment 2
[0028] In the normal production process, because the heating roller bears a certain working pressure, and the displacement sensor is installed on the bearing seat, it is impossible to know whether the actual gap value is the same as the value displayed by the displacement sensor. At this time, it is necessary to check the gap during use. To measure, the measurement method is as follows:
[0029] 1. Adjust the gap between the paired heating rollers, and the display value of the displacement sensors at both ends is S3.
[0030] 2. Start the heating roller to make it work normally. At this time, the working temperature of the heating roller is F1 degrees Celsius.
[0031] 3. Cut off two pieces of pure lead wire with a diameter of 6mm and equal length, and put them into the left roller pillow 1 and the right roller pillow 2 at the two ends of the heating roller at the same time (such as figure 2 As shown), let the lead wire rotate together with the heating roller (do not drag th...
PUM
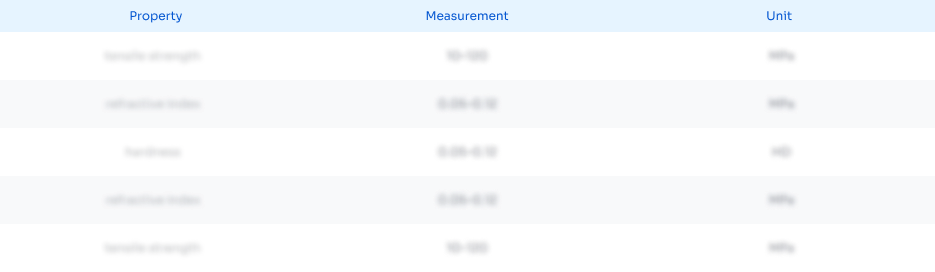
Abstract
Description
Claims
Application Information

- R&D Engineer
- R&D Manager
- IP Professional
- Industry Leading Data Capabilities
- Powerful AI technology
- Patent DNA Extraction
Browse by: Latest US Patents, China's latest patents, Technical Efficacy Thesaurus, Application Domain, Technology Topic, Popular Technical Reports.
© 2024 PatSnap. All rights reserved.Legal|Privacy policy|Modern Slavery Act Transparency Statement|Sitemap|About US| Contact US: help@patsnap.com