3D printing forming method of continuous fiber reinforced member
A continuous fiber, 3D printing technology, applied in the field of 3D printing, can solve the problems of low printing success rate, easy to block the nozzle, and low production efficiency, and achieve the goals of wide applicability and combination, improved efficiency, and improved quality and performance Effect
- Summary
- Abstract
- Description
- Claims
- Application Information
AI Technical Summary
Problems solved by technology
Method used
Image
Examples
Embodiment 1
[0046] The invention provides a 3D printing molding method of a continuous fiber reinforced component, comprising the following steps:
[0047] Step 1. The photosensitive resin and the continuous fiber are fully contacted inside the extrusion head, so that the surface of the continuous fiber is wrapped with the photosensitive resin to form a composite precursor;
[0048] Step 2. Use the FDM-3D printing platform to synchronously carry out component molding;
[0049] Step 3. Under light conditions, the photosensitive resin is cross-linked and cured during the printing process, and the composite reinforcement of the continuous fiber and the photosensitive resin is completed, such as image 3 As shown, a continuous fiber reinforced component is obtained;
[0050] Such as Figure 1~2 As shown, the extrusion head includes a wire feeding device 1, a shearing device 2, an extrusion cavity 3 and a nozzle 4 arranged in sequence from top to bottom, and the wire feeding device 1 is prov...
Embodiment 2
[0055] Embodiment 2 (tough continuous fiber printing)
[0056] In this example, tough continuous fiber is used as the object, and continuous glass fiber is used, which is hard, has a certain degree of plasticity, and has a certain non-axial strength at the same time. It can directly use the FDM-3D printing platform for supply and printing. The specific steps are:
[0057] (1) Pass the continuous glass fiber through the first feeding end 101 on the frame 102, pass between the driving wheel 103 and the driven wheel 105 and clamp it, and the driving wheel 103 rotates under the control of the driving circuit to drive the continuous fiber forward Feeding, the fiber enters the inside of the extrusion cavity 3 through the extrusion cavity feed port 302;
[0058] (2) Load the peristaltic pump with photosensitive resin, connect the conduit to the second feed port 301, and fill the inside of the extrusion head with photosensitive resin;
[0059] (3) Load the printed device model into t...
Embodiment 3
[0061] Embodiment 3 (non-tough continuous fiber printing coated with photosensitive resin)
[0062] In this example, non-tough continuous fibers are used as the object, and continuous carbon fibers are used, which are soft and cannot be extruded progressively by wire feeding devices. Surface coating treatment is required to make them have a certain toughness, and then proceed in the way of tough continuous fibers. Print, the specific steps are:
[0063] (1) Put the continuous carbon fiber into the photosensitive resin of the same material as the printing for soaking to ensure full contact between the carbon fiber and the photosensitive resin;
[0064] (2) After the soaking is completed, straighten the carbon fiber and place it on the table, and use a light source to illuminate it, so that the photosensitive resin on the surface is cured to complete the toughness treatment;
[0065] (3) Finally, the process of printing and forming the tough continuous fiber is carried out, and...
PUM
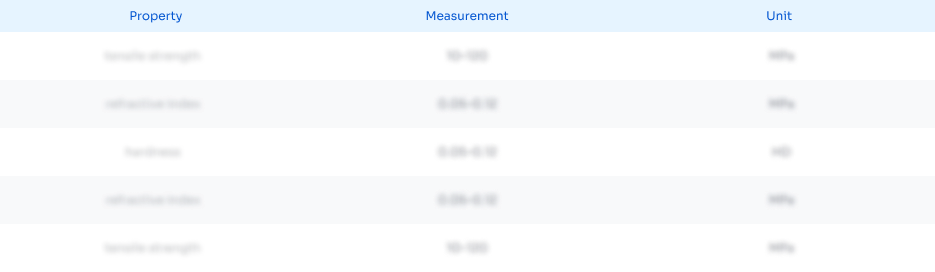
Abstract
Description
Claims
Application Information

- R&D
- Intellectual Property
- Life Sciences
- Materials
- Tech Scout
- Unparalleled Data Quality
- Higher Quality Content
- 60% Fewer Hallucinations
Browse by: Latest US Patents, China's latest patents, Technical Efficacy Thesaurus, Application Domain, Technology Topic, Popular Technical Reports.
© 2025 PatSnap. All rights reserved.Legal|Privacy policy|Modern Slavery Act Transparency Statement|Sitemap|About US| Contact US: help@patsnap.com