High-strength light gypsum keel and application
A high-strength, keel technology, applied to building components, walls, buildings, etc., can solve the problems of low strength and high weight of gypsum keels, and achieve high flexural strength, light weight, and improved strength
- Summary
- Abstract
- Description
- Claims
- Application Information
AI Technical Summary
Problems solved by technology
Method used
Image
Examples
Embodiment 1
[0025] Embodiment 1 plaster keel
[0026] Raw materials: 80kg of industrial by-product plaster of paris, 8kg of light calcium carbonate, 8kg of slag powder, 20kg of porous polypropylene fiber, 3kg of sodium lignosulfonate, 1kg of sulfamate superplasticizer, and 8kg of cement.
[0027] The preparation process of the modified polypropylene fiber is as follows: take a polypropylene slice with a melt index of 30-50, add 5% of its mass of nano-gypsum powder and 0.1% of its mass of sodium stearate, and mix them in a screw extruder. Extrude to make blended fibers; soak the blended fibers in 5% hydrochloric acid solution for 4 hours, take them out, wash with water, and dry to make porous polypropylene fibers.
[0028] Preparation:
[0029] (1) Mix industrial re-production plaster of paris with light calcium carbonate, add water to make a suspension with a slurry concentration of 15%; add a reinforcing agent to the suspension and stir evenly, then stir and react at 80-90°C for 0.5h ,...
Embodiment 2
[0034] Embodiment 2 plaster keel
[0035] Raw materials: 65kg of industrial by-product plaster of paris, 9kg of light calcium carbonate, 7kg of slag powder, 24kg of porous polypropylene fiber, 2.4kg of potassium tartrate, 1.5kg of sulfamate-based superplasticizer, and 6kg of cement.
[0036] The preparation process of the modified polypropylene fiber is as follows: take a polypropylene slice with a melt index of 30-50, add 4% of its mass of nano-gypsum powder and 0.2% of its mass of sodium stearate and mix them in a screw extruder Extrude to make blended fibers; soak the blended fibers in 5% hydrochloric acid solution for 4 hours, take them out, wash with water, and dry to make porous polypropylene fibers.
[0037] Preparation:
[0038] (1) Mix industrial re-production plaster of paris with light calcium carbonate, add water to make a suspension with a slurry concentration of 15%; add a reinforcing agent to the suspension and stir evenly, then stir and react at 80-90°C for 0....
Embodiment 3
[0043] Embodiment 3 plaster keel
[0044] Raw materials: 60kg of industrial by-product plaster of paris, 10kg of light calcium carbonate, 6kg of slag powder, 30kg of porous polypropylene fiber, 2kg of sodium lignosulfonate, 2kg of sulfamate-based superplasticizer, and 4kg of cement.
[0045] The preparation process of the modified polypropylene fiber is as follows: take a polypropylene slice with a melt index of 30-50, add 5% of its mass of nano-gypsum powder and 0.3% of its mass of sodium stearate and mix them in a screw extruder Extrude to make blended fibers; soak the blended fibers in 5% hydrochloric acid solution for 4 hours, take them out, wash with water, and dry to make porous polypropylene fibers.
[0046] Preparation:
[0047](1) Mix industrial re-production plaster of paris with light calcium carbonate, add water to make a suspension with a slurry concentration of 15%; add a reinforcing agent to the suspension and stir evenly, then stir and react at 80-90°C for 0.5...
PUM
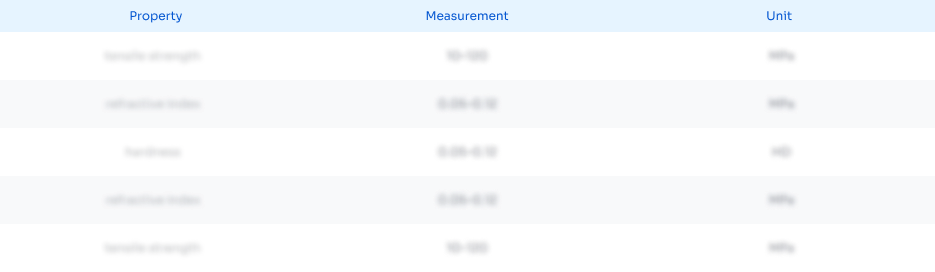
Abstract
Description
Claims
Application Information

- R&D Engineer
- R&D Manager
- IP Professional
- Industry Leading Data Capabilities
- Powerful AI technology
- Patent DNA Extraction
Browse by: Latest US Patents, China's latest patents, Technical Efficacy Thesaurus, Application Domain, Technology Topic, Popular Technical Reports.
© 2024 PatSnap. All rights reserved.Legal|Privacy policy|Modern Slavery Act Transparency Statement|Sitemap|About US| Contact US: help@patsnap.com