Method for producing moulded part and feeder insert for use in such method
A technology for inserts and molded parts, applied in the field of manufacturing molded parts, can solve the problems of expensive reprocessing, unusable castings, irregular castings, etc., and achieves the effect of improving reliability and avoiding damage
- Summary
- Abstract
- Description
- Claims
- Application Information
AI Technical Summary
Problems solved by technology
Method used
Image
Examples
Embodiment Construction
[0058] exist figure 1 In , a riser insert 2 according to the invention is shown in a cross-sectional view according to a first embodiment. The riser insert 2 has a riser body 4 comprising a riser cavity 6 for receiving liquid metal. The riser insert 2 has a riser opening 10 at the first end 8 on the riser body 4, by means of which a riser opening can be established with the molding 26 ( image 3 ) The connection of the molding cavity 30 in. The riser body 4 is closed at the opposite second end 12 and has a side wall 14 extending between the first end 8 and the second end 12 . A filter element 16 is arranged in the feeder cavity 6 , by means of which filter element the material flowing through the feeder insert 2 is cleaned. In the present embodiment, even though the feeder body is constituted by a plurality of single parts such as the feeder element 18 and the cover 20, the feeder main body 4 is constituted in one piece. In the present case, one-piece is to be understood a...
PUM
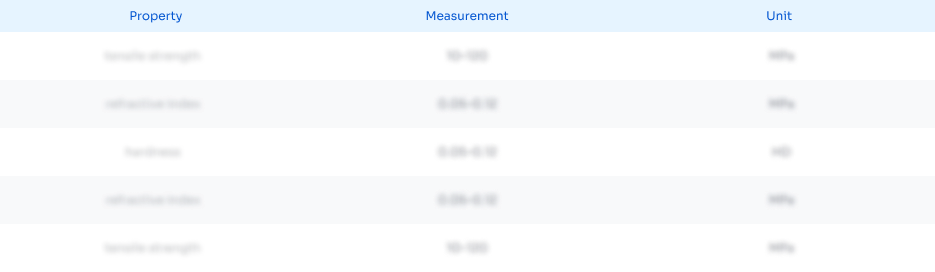
Abstract
Description
Claims
Application Information

- R&D Engineer
- R&D Manager
- IP Professional
- Industry Leading Data Capabilities
- Powerful AI technology
- Patent DNA Extraction
Browse by: Latest US Patents, China's latest patents, Technical Efficacy Thesaurus, Application Domain, Technology Topic, Popular Technical Reports.
© 2024 PatSnap. All rights reserved.Legal|Privacy policy|Modern Slavery Act Transparency Statement|Sitemap|About US| Contact US: help@patsnap.com