Digital printing process of artificial cellulose fiber fabric
An artificial cellulose and digital printing technology, applied in the field of textile printing, can solve the problems of fabric yellowing, achieve the effect of increased whiteness value of fabric, simple process, and strong three-dimensional effect
- Summary
- Abstract
- Description
- Claims
- Application Information
AI Technical Summary
Problems solved by technology
Method used
Examples
Embodiment 1
[0024] Prepare 100g of digital printing pretreatment agent:
[0025] Weigh 11g of urea, 1g of baking soda, 0.8g of antioxidant, add 85.92g of water, and stir on a stirrer. After all the ingredients are dissolved, weigh 2g of sodium carboxymethylcellulose and slowly add it under stirring. Continue to stir for 2 hours, stop stirring, and puff for 8 hours for later use.
[0026] Padding pretreatment agent: padding car pressure 2kg, one dipping and one rolling, the excess rate is 78%, and drying after padding is completed, and the drying temperature is ≤100°C.
[0027] After digital printing is normally printed, place the viscose fabric in a steamer to steam at a steaming temperature of 102-105°C for 8 minutes, wash in cold water, wash in hot water, wash in cold water, and dry.
Embodiment 2
[0039] Formulating digital printing pretreatment agent:
[0040] Weigh 7 parts of urea, 0.5 parts of baking soda, and 0.5 parts of ascorbic acid, add deionized water, stir, and weigh 1 part of hydroxypropyl methylcellulose after all the ingredients are dissolved, and slowly add hydroxypropyl methylcellulose during the stirring process. For methyl cellulose, continue to stir for 1-2 hours until the paste is fully dispersed, stop stirring, and puff for 6-10 hours for use. The viscosity of the digital printing pretreatment agent is less than 20000mPa·S. .
[0041] Padding pretreatment agent: under the condition of 2kg pressure, one dipping and one rolling, the excess rate is 100%, and drying after padding, the drying temperature is ≤100°C.
[0042] After normal digital printing, place the viscose fiber fabric in a steamer to steam at a steaming temperature of 105°C and a steaming time of 7 minutes. The washing process includes: cold water washing→hot water washing→cold water was...
Embodiment 3
[0044] Formulating digital printing pretreatment agent:
[0045] Weigh 25 parts of urea, 2 parts of baking soda, and 2 parts of astaxanthin, add deionized water, stir, and weigh 3 parts of hydroxyethyl cellulose after all the ingredients are dissolved, and slowly add hydroxyethyl cellulose during the stirring process. For cellulose, continue to stir for 1-2 hours until the paste is fully dispersed, stop stirring, and puff for 6-10 hours for use. The viscosity of the digital printing pretreatment agent is less than 20000mPa·S. .
[0046] Padding pretreatment agent: under the condition of 2kg pressure, one dipping and one rolling, the excess rate is 70%, and drying after padding, the drying temperature is ≤100°C.
[0047] After normal digital printing, place the viscose fiber fabric in a steamer to steam at a steaming temperature of 102°C and a steaming time of 10 minutes. The washing process includes: cold water washing→hot water washing→cold water washing, and finally drying....
PUM
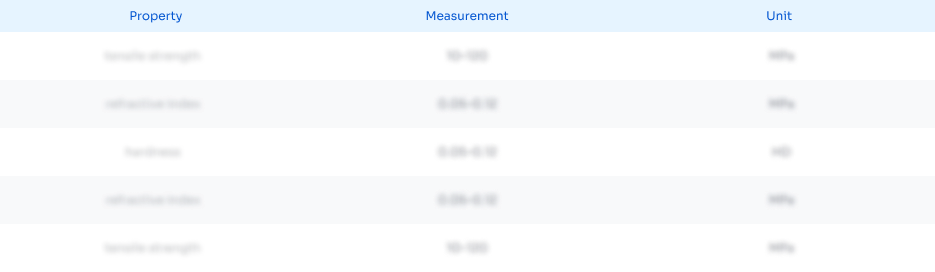
Abstract
Description
Claims
Application Information

- Generate Ideas
- Intellectual Property
- Life Sciences
- Materials
- Tech Scout
- Unparalleled Data Quality
- Higher Quality Content
- 60% Fewer Hallucinations
Browse by: Latest US Patents, China's latest patents, Technical Efficacy Thesaurus, Application Domain, Technology Topic, Popular Technical Reports.
© 2025 PatSnap. All rights reserved.Legal|Privacy policy|Modern Slavery Act Transparency Statement|Sitemap|About US| Contact US: help@patsnap.com