Working method of intelligent stamping device
A technology of stamping device and working method, applied in the field of stamping device, to achieve the effect of ensuring stamping efficiency, ensuring stamping effect, and small stamping force
- Summary
- Abstract
- Description
- Claims
- Application Information
AI Technical Summary
Problems solved by technology
Method used
Image
Examples
specific Embodiment approach 1
[0043] Combine below Figure 1-16 Describe this embodiment, an intelligent stamping device, including a chassis 1, a support bracket 2, a stamping platform 3, a pressing mechanism 4, a clamping mechanism 5, a lifting gear 6, a lifting rack 7, a power mechanism 8, and a transmission mechanism I9 , transmission mechanism II 10, stamping crank 11, stamping connecting rod 12, stamping die 13 and tensioning mechanism 14, the support bracket 2 is fixedly connected to the chassis 1, the stamping platform 3 is fixedly connected to the support bracket 2, and the compression mechanism 4. It is fixedly connected to the base frame 1. There are two clamping mechanisms 5. One end of the two clamping mechanisms 5 is both slidably connected to the stamping platform 3, and the other ends of the two clamping mechanisms 5 are both slidably connected to the pressing platform 3. On the mechanism 4, the lifting gear 6 is rotatably connected to the support bracket 2, one side of the lifting gear 6 i...
specific Embodiment approach 2
[0053] Combine below Figure 1-16 Describe this embodiment, this embodiment will further explain the eighth embodiment, the stamping crank 11 includes a crankshaft 11-1 and a stamping pulley 11-2, and the two ends of the crankshaft 11-1 are respectively rotatably connected to two supporting plates II2 -4, the crankshaft 11-1 is fixedly connected with a stamping pulley 11-2, the stamping pulley 11-2 and the drive pulley II 10-5 are connected through a belt drive, and one end of the stamping connecting rod 12 is hinged to the crankshaft 11-1 Eccentric position, the other end of the stamping connecting rod 12 is hinged on the stamping die 13, the stamping die 13 is located on the upper side of the stamping platform 3, and the two ends of the stamping die 13 are respectively slidingly connected in two vertical waist holes II2-5; the transmission belt Wheel II 10-5 drives the stamping pulley 11-2 to rotate around its own axis, the stamping pulley 11-2 drives the crankshaft 11-1 to ...
specific Embodiment approach 3
[0055] Combine below Figure 1-16 Describe this embodiment, this embodiment will further explain Embodiment 9, the tensioning mechanism 14 includes a tensioning bracket 14-1, a tensioning sliding column 14-2 and a tensioning pulley 14-3, and the tensioning bracket 14 -1 is fixedly connected with a tensioning sliding column 14-2, and the tensioning sliding column 14-2 is slidably connected to the tensioning support plate 4-5, and the tensioning sliding column 14-2 is covered with a compression spring II, and the compression spring II Located between the tension support 14-1 and the tension support plate 4-5, the lower end of the tension support 14-1 is rotatably connected with a tension pulley 14-3, the lower end of the tension pulley 14-3 and the stamping pulley 11-2 is in contact with the transmission belt between the transmission pulley II 10-5; when the transmission ratio between the transmission mechanism I9 and the transmission mechanism II10 changes, the relative distanc...
PUM
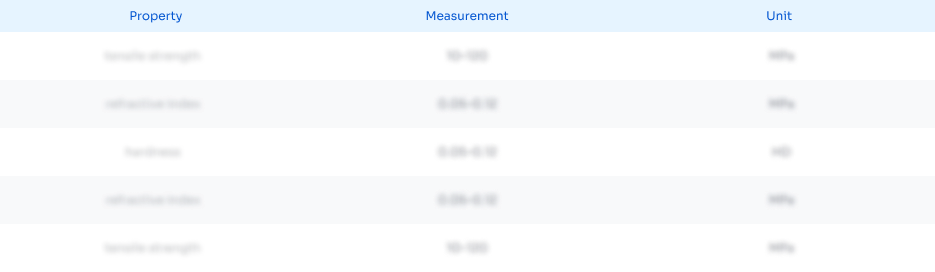
Abstract
Description
Claims
Application Information

- R&D
- Intellectual Property
- Life Sciences
- Materials
- Tech Scout
- Unparalleled Data Quality
- Higher Quality Content
- 60% Fewer Hallucinations
Browse by: Latest US Patents, China's latest patents, Technical Efficacy Thesaurus, Application Domain, Technology Topic, Popular Technical Reports.
© 2025 PatSnap. All rights reserved.Legal|Privacy policy|Modern Slavery Act Transparency Statement|Sitemap|About US| Contact US: help@patsnap.com