Fly ash multi-stage recycling treatment device and process
A treatment device and a treatment process technology, which are applied in the field of fly ash multi-stage reuse treatment devices, can solve the problems such as the inability to truly realize the resource utilization of solid and hazardous waste, the ineffective utilization of light fly ash, etc., and reduce energy consumption. Effect
- Summary
- Abstract
- Description
- Claims
- Application Information
AI Technical Summary
Problems solved by technology
Method used
Image
Examples
Embodiment 1
[0021] Embodiment 1: as figure 1 As shown, a fly ash multi-stage recycling treatment device includes a first-stage rotary kiln 1, a second-stage rotary kiln 2, a crystallization device 3, a No. 1 high-temperature dust collector 4, and an exhaust gas treatment device 5. The first-stage rotary kiln 1 and the second-stage rotary kiln The tail of the kiln 2 is equipped with an exhaust port and a material discharge port. The exhaust port 1.1 of the first section of the rotary kiln is connected to the air inlet 4.1 of the No. 1 high-temperature dust collector, and the exhaust port 4.2 of the No. 1 high-temperature dust collector is connected to the waste gas treatment device 5. The dust discharge port 4.3 of the No. high temperature dust collector is connected with the collection device 6, the discharge port 1.2 of the first-stage rotary kiln is connected with the feed port 2.1 of the second-stage rotary kiln, and the exhaust port 2.2 of the second-stage rotary kiln is connected with...
Embodiment 2
[0022] Example 2: A multi-stage recycling process for fly ash. After mixing fly ash and clay, it enters the first-stage rotary kiln 1. The temperature of the first-stage rotary kiln 1 is controlled at 600° C., and the residence time of the first-stage rotary kiln 1 is 0.5 hours. After the first-stage rotary kiln 1 is fired, the dust-containing waste gas of the first-stage rotary kiln 1 is dedusted, and the dust after dust removal is collected to prepare lightweight bricks, and the waste gas after dust removal is subjected to waste gas treatment; the fired materials of the first-stage rotary kiln 1 are sent to the second The temperature of the first stage rotary kiln 2 and the second stage rotary kiln 2 is controlled at 1100°C, and the residence time of the second stage rotary kiln 2 is 1 hour. After firing, the finished ceramsite is obtained. It is discharged into the crystallization device 3 for heat exchange crystallization, and the crystallized material is discharged after c...
Embodiment 3
[0023] Example 3: A fly ash multi-stage recycling treatment process, the fly ash and clay are mixed and then enter a rotary kiln, the temperature of the first rotary kiln 1 is controlled at 620 °C, and the residence time of the first rotary kiln 1 is 0.7 hours After the first section of rotary kiln 1 is fired, the dust-containing waste gas of the first section of rotary kiln is dedusted, and the dust after dust removal is used to prepare lightweight bricks, and the exhaust gas after dust removal is treated for waste gas; The first-stage rotary kiln, the temperature of the second-stage rotary kiln 2 is controlled at 1200°C, and the residence time of the second-stage rotary kiln 2 is 1.5 hours. Enter the crystallization device 3 for heat exchange crystallization, and discharge the crystallized material after crystallization. The temperature in the crystallization device 3 is 400°C. The dust-laden flue gas discharged from the crystallization device 3 is used for heating the first...
PUM
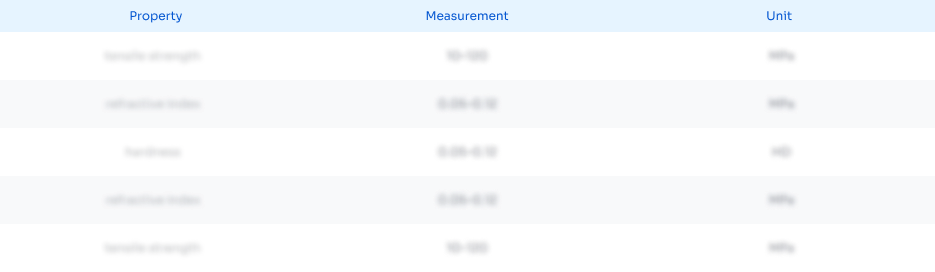
Abstract
Description
Claims
Application Information

- R&D
- Intellectual Property
- Life Sciences
- Materials
- Tech Scout
- Unparalleled Data Quality
- Higher Quality Content
- 60% Fewer Hallucinations
Browse by: Latest US Patents, China's latest patents, Technical Efficacy Thesaurus, Application Domain, Technology Topic, Popular Technical Reports.
© 2025 PatSnap. All rights reserved.Legal|Privacy policy|Modern Slavery Act Transparency Statement|Sitemap|About US| Contact US: help@patsnap.com