A high-precision etching transfer method for micro-nano structure patterns on curved substrates
A micro-nano structure, high-precision technology, applied in the direction of micro-structure technology, micro-structure devices, manufacturing micro-structure devices, etc., can solve the problem of poor uniformity of etching depth and other problems
- Summary
- Abstract
- Description
- Claims
- Application Information
AI Technical Summary
Problems solved by technology
Method used
Image
Examples
Embodiment 1
[0051] A high-precision reactive ion etching transfer method for micro-nano structure patterns on a curved substrate of quartz material, the specific steps are as follows:
[0052] Step (1), using magnetron sputtering on the curved substrate of concave quartz material, deposits a 100 nanometer thick Cr film; the conductive film 15 in the step (1) is a Cr film;
[0053] Step (2), prepare a layer of photoresist with glue coating equipment on the curved surface substrate of the quartz material coated with Cr thin film, and then prepare a predetermined photoresist on the Cr thin film on the curved surface substrate by photolithography. Resist microstructure pattern---a concentric ring array with radial connecting lines;
[0054] Step (3), by using the method of chromium removal liquid wet etching, the photoresist pattern etching is transferred to the Cr conductive film on the curved substrate, forming a Cr film microstructure pattern consistent with the photoresist layer , as a m...
Embodiment 2
[0060] A high-precision reactive ion etching transfer method for a micro-nano structure pattern on a silicon curved substrate, using an electron beam to evaporate an Au film on a convex silicon curved substrate, the specific steps are as follows:
[0061] Step (1), using an electron beam to deposit an Au film with a thickness of 5 nanometers on the curved substrate of the convex silicon material;
[0062] Step (2), prepare a layer of photoresist with glue coating equipment on the silicon curved substrate coated with Au film, and then prepare it on the conductive Au thin film on the convex silicon material curved substrate by laser direct writing method Produce a predetermined photoresist microstructure pattern, such as a network structure with a period of 50 microns;
[0063] Step (3), by ion beam etching, the photoresist pattern etching is transferred to the Au conductive film on the silicon curved substrate to form the Au conductive film microstructure pattern consistent wit...
PUM
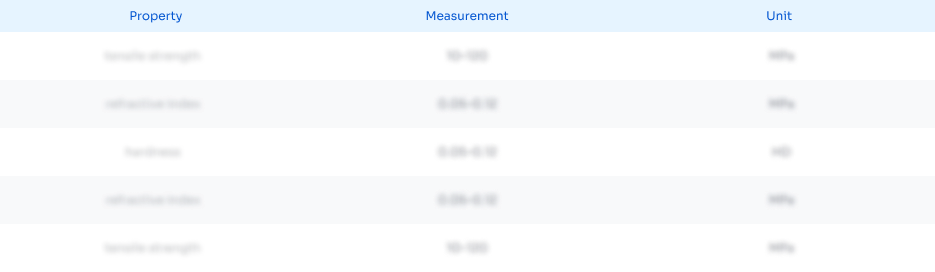
Abstract
Description
Claims
Application Information

- R&D
- Intellectual Property
- Life Sciences
- Materials
- Tech Scout
- Unparalleled Data Quality
- Higher Quality Content
- 60% Fewer Hallucinations
Browse by: Latest US Patents, China's latest patents, Technical Efficacy Thesaurus, Application Domain, Technology Topic, Popular Technical Reports.
© 2025 PatSnap. All rights reserved.Legal|Privacy policy|Modern Slavery Act Transparency Statement|Sitemap|About US| Contact US: help@patsnap.com