Robot power joint with turbulent flow heat dissipation structure and robot
A technology of heat dissipation structure and joints, applied in the field of robots, can solve the problems of complex structure of heat dissipation device, incompatibility with the lightweight, compact, and large size of bionic robots, so as to enhance the convective heat dissipation capability, reduce the transient temperature rise, increase the The effect of heat dissipation area
- Summary
- Abstract
- Description
- Claims
- Application Information
AI Technical Summary
Problems solved by technology
Method used
Image
Examples
Embodiment Construction
[0032] In order to make the purpose, technical solutions and advantages of the embodiments of the present invention more clear, the embodiments of the present invention will be further described in detail below in conjunction with the accompanying drawings. Here, the exemplary embodiments and descriptions of the present invention are used to explain the present invention, but not to limit the present invention.
[0033] Here, it should be noted that, in order to avoid obscuring the present invention due to unnecessary details, only the structures and / or processing steps that are closely related to the solution according to the present invention are shown in the drawings, while those related to the present invention are omitted. Invent other details that don't really matter.
[0034] It should be emphasized that the term "comprises / comprises / has" when used herein refers to the presence of a feature, element, step or component, but does not exclude the presence or addition of on...
PUM
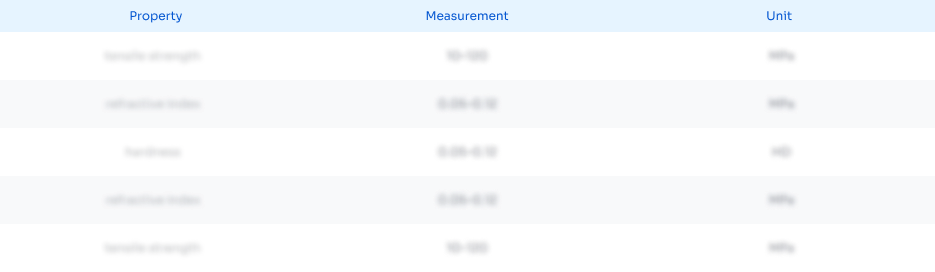
Abstract
Description
Claims
Application Information

- R&D
- Intellectual Property
- Life Sciences
- Materials
- Tech Scout
- Unparalleled Data Quality
- Higher Quality Content
- 60% Fewer Hallucinations
Browse by: Latest US Patents, China's latest patents, Technical Efficacy Thesaurus, Application Domain, Technology Topic, Popular Technical Reports.
© 2025 PatSnap. All rights reserved.Legal|Privacy policy|Modern Slavery Act Transparency Statement|Sitemap|About US| Contact US: help@patsnap.com