Bulk material unmanned loading control method, system and device based on multi-line laser radar
A multi-line laser and radar technology, used in control/regulation systems, flow control using electrical devices, controllers with specific characteristics, etc. Stable loading quality and other issues
- Summary
- Abstract
- Description
- Claims
- Application Information
AI Technical Summary
Problems solved by technology
Method used
Image
Examples
Embodiment 1
[0046] This embodiment provides a bulk material unmanned loading control method based on multi-line laser radar, such as figure 1 shown, including:
[0047] S1: Obtain the 3D point cloud data of the carriage collected by the multi-line laser radar in real time, establish the 3D data model of the carriage, and calculate the real-time position coordinates of the carriage;
[0048] S2: After detecting that the compartment enters the set position of the bulk material yard, it is judged that a vehicle enters, and vehicle identification is started;
[0049] S3: Calculate the length, width and height of the compartment according to the real-time three-dimensional point cloud data of the compartment, and set the target material accumulation height of the compartment to be loaded according to the weight of the material to be loaded;
[0050] S4: When it is judged that the compartment moves to the loading position, and it is detected that the compartment does not deviate from the drivi...
Embodiment 2
[0086] This embodiment provides a bulk material unmanned loading control system based on multi-line laser radar, including:
[0087] The 3D modeling module is used to obtain the 3D point cloud data of the car collected by the multi-line laser radar in real time, and establish the 3D data model of the car;
[0088] The identification and judgment module is used to calculate the real-time position coordinates of the carriage. When it is detected that the carriage enters the set position of the bulk material yard, it is judged that there is a vehicle entering, and the vehicle identification is started;
[0089] The parameter setting module is used to calculate the length, width and height of the carriage according to the real-time three-dimensional point cloud data of the carriage, and set the target material accumulation height of the carriage to be loaded according to the weight of the material to be loaded;
[0090] The loading start module is used to start the unmanned unifor...
Embodiment 3
[0104] This embodiment provides a bulk material unmanned loading control device based on multi-line laser radar, such as image 3 As shown, comprising: multi-line laser radar, background server and PLC controller, described background server is arranged with point cloud database;
[0105] The multi-line laser radar is installed at a set height on the side of the carriage, and is used to collect the three-dimensional point cloud data of the carriage in real time, and store it in the point cloud database of the background server;
[0106] The background server is used to realize the control method described in claim 1;
[0107] The PLC controller communicates with the background server to obtain the three-dimensional data information of the compartment analyzed by the background server, and adopts PID control to adjust the material flow in the mobile loading operation.
[0108] The multi-line laser radar adopts the 360-degree circular scanning method of multiple laser beams to ...
PUM
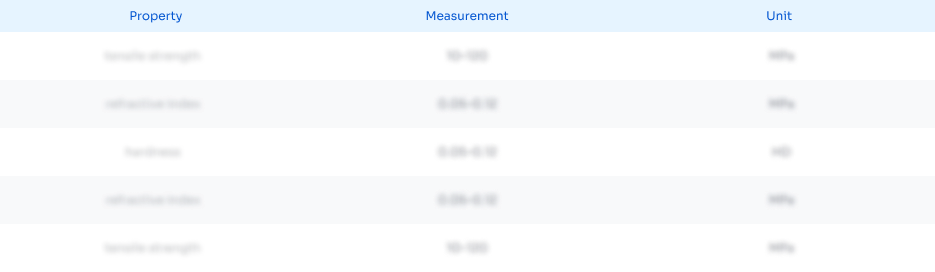
Abstract
Description
Claims
Application Information

- R&D
- Intellectual Property
- Life Sciences
- Materials
- Tech Scout
- Unparalleled Data Quality
- Higher Quality Content
- 60% Fewer Hallucinations
Browse by: Latest US Patents, China's latest patents, Technical Efficacy Thesaurus, Application Domain, Technology Topic, Popular Technical Reports.
© 2025 PatSnap. All rights reserved.Legal|Privacy policy|Modern Slavery Act Transparency Statement|Sitemap|About US| Contact US: help@patsnap.com