Thermodynamic system of steam turbine and method of improving efficiency thereof
A thermal system and steam turbine technology, applied in steam engine installations, mechanical equipment, machines/engines, etc., can solve the problem of high humidity, reduce the proportion, improve the availability, and reduce the total amount of exhaust steam.
- Summary
- Abstract
- Description
- Claims
- Application Information
AI Technical Summary
Problems solved by technology
Method used
Image
Examples
Embodiment Construction
[0032] Such as figure 1 , Embodiment 1 of the present invention, (1+1+1) includes a first-stage high-pressure cylinder 1 , a first-stage medium-pressure cylinder 2 and a first-stage low-pressure cylinder 5 . The main steam is directly input into the first-stage high-pressure cylinder 1, then into the first-stage medium-pressure cylinder 2, then passes through the first-stage water-steam separator 3 and the first-stage reheater 4, and then enters the first-stage first low-pressure cylinder 5, and finally becomes exhausted steam sent to the condenser. Among them, the parameter selection of the first-stage reheater 4 should finally reduce the total amount of steam entering the first low-pressure cylinder of the first stage by 10%-15%. When the humidity of the wet steam in the medium-pressure cylinder and the first-stage low-pressure cylinder reaches 15%, it is discharged to the reheater for dehumidification and heating.
[0033] Such as figure 2 , embodiment two of the presen...
PUM
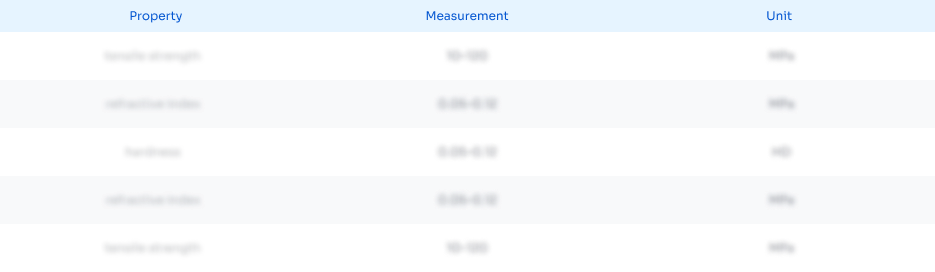
Abstract
Description
Claims
Application Information

- Generate Ideas
- Intellectual Property
- Life Sciences
- Materials
- Tech Scout
- Unparalleled Data Quality
- Higher Quality Content
- 60% Fewer Hallucinations
Browse by: Latest US Patents, China's latest patents, Technical Efficacy Thesaurus, Application Domain, Technology Topic, Popular Technical Reports.
© 2025 PatSnap. All rights reserved.Legal|Privacy policy|Modern Slavery Act Transparency Statement|Sitemap|About US| Contact US: help@patsnap.com