Creep-fatigue life design method for complex geometric structural member
A technology of geometric structure and design method, applied in geometric CAD, computer-aided design, design optimization/simulation, etc., can solve the problems of negligible creep damage, creep damage, failure to reflect service temperature field, etc.
- Summary
- Abstract
- Description
- Claims
- Application Information
AI Technical Summary
Problems solved by technology
Method used
Image
Examples
Embodiment Construction
[0062] The present invention will be further described below in conjunction with specific embodiments. It should be understood that the following examples are only used to illustrate the present invention but not to limit the scope of the present invention.
[0063] In actual working conditions, in addition to the fatigue load caused by centrifugal force, complex geometrical parts such as aviation turbine disks are always in the harsh environment of high temperature and high pressure, so the role of creep effect in fatigue cycle load is also very obvious. Therefore the present invention provides a kind of creep fatigue life prediction simulation method based on ABAQUS, this method considers the thermo-mechanical load interaction, gives the actual working temperature and load spectrum to the structure, gives the constitutive parameters of the material under different temperatures, based on the stability The non-uniform cyclic constitutive equation of the state stress-strain res...
PUM
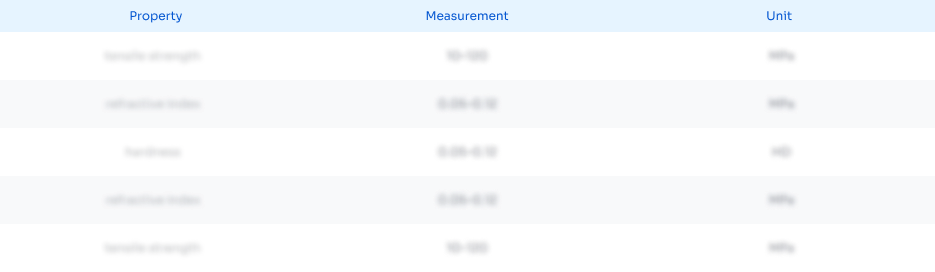
Abstract
Description
Claims
Application Information

- Generate Ideas
- Intellectual Property
- Life Sciences
- Materials
- Tech Scout
- Unparalleled Data Quality
- Higher Quality Content
- 60% Fewer Hallucinations
Browse by: Latest US Patents, China's latest patents, Technical Efficacy Thesaurus, Application Domain, Technology Topic, Popular Technical Reports.
© 2025 PatSnap. All rights reserved.Legal|Privacy policy|Modern Slavery Act Transparency Statement|Sitemap|About US| Contact US: help@patsnap.com