Manufacturing method of colorized denim yarn and fabric and garment manufactured through yarn
A production method and color technology, applied in the direction of dyeing method, yarn, dry cleaning fiber products, etc., can solve the problems of serious staining, poor wet rubbing fastness, poor multi-fiber color fastness, etc. Excellent soaping fastness, less sewage and polluting gases, and easy environmental treatment
- Summary
- Abstract
- Description
- Claims
- Application Information
AI Technical Summary
Problems solved by technology
Method used
Image
Examples
Embodiment 1
[0032] A kind of manufacture method of blue denim yarn, comprises the steps:
[0033] The first step is the pre-dyeing treatment of cotton loose fibers, which is used to remove grease and wax on cotton loose fibers, enhance the permeability of cotton loose fibers, and improve the dye uptake rate during dyeing;
[0034] The second step, cotton loose fiber dyeing: add dye, that is, vat dye leuco dye solution, heat at a heating rate of 0.5°C / min, when the temperature reaches 50°C, keep warm for 70min, and keep warm for 20 minutes and 40 minutes Add the dyeing accelerator in 10 minutes, the dyeing accelerator is preferably Yuanming powder, and the consumption of twice adding the dyeing accelerator is 15g / L;
[0035] The third step is post-dyeing treatment of cotton loose fiber;
[0036] The fourth step, blending and spinning: dyed cotton loose fibers and undyed cotton loose fibers are mixed and spun, wherein the dyed cotton loose fibers account for 50%.
[0037] Among them, dyei...
Embodiment 2
[0039] A kind of manufacture method of blue denim yarn, comprises the steps:
[0040] The first step is the pre-dyeing treatment of cotton loose fiber, which is used to remove the grease and wax on cotton loose fiber, so as to improve the dye uptake rate during dyeing;
[0041] The second step, cotton loose fiber dyeing: add dye, i.e. vat dye leuco dye solution, heat up at a heating rate of 0.5°C / min, when the temperature reaches 60°C, add a dyeing accelerator, keep it warm for 50min, and then heat up to Add dye accelerator at 80°C and keep warm for 20min. The dyeing accelerator is preferably a mixture of sodium sulfate and sodium chloride blended in a 1:1 ratio. In this embodiment, the first addition of the dyeing accelerator is 10 g / L, and the second addition is 20 g / L;
[0042] The third step is the post-dyeing treatment of cotton loose fiber;
[0043] The fourth step, blending and spinning: dyed cotton loose fibers and undyed cotton loose fibers are mixed and spun, where...
Embodiment 3
[0045] A kind of manufacture method of blue denim yarn, comprises the steps:
[0046] The first step is the pre-dyeing treatment of cotton loose fiber, which is used to remove the grease and wax on cotton loose fiber, so as to improve the dye uptake rate during dyeing;
[0047] The second step, cotton loose fiber dyeing: add dye, i.e. vat dye leuco dye solution, heat up at a heating rate of 0.5°C / min, when the temperature reaches 60°C, add a dyeing accelerator, keep it warm for 50min, and then heat up to Add dye accelerator at 85°C and keep warm for 10min. The dyeing accelerator is preferably a mixture of sodium sulfate and sodium chloride blended in a 4:1 ratio. In this embodiment, the first addition of the dyeing accelerator is 10 g / L, and the second addition is 15 g / L;
[0048] The third step is the post-dyeing treatment of cotton loose fiber;
[0049] The fourth step, blending and spinning: dyed cotton loose fibers and undyed cotton loose fibers are mixed and spun, where...
PUM
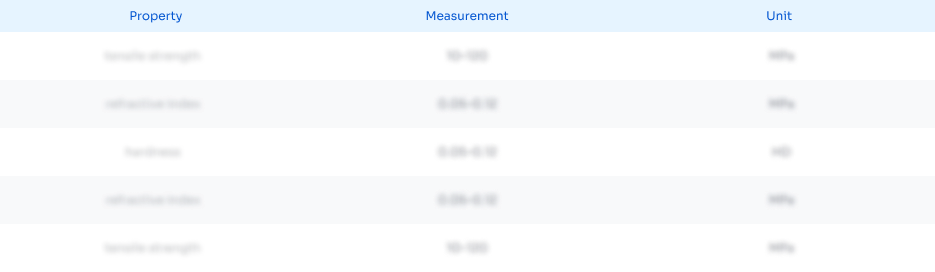
Abstract
Description
Claims
Application Information

- Generate Ideas
- Intellectual Property
- Life Sciences
- Materials
- Tech Scout
- Unparalleled Data Quality
- Higher Quality Content
- 60% Fewer Hallucinations
Browse by: Latest US Patents, China's latest patents, Technical Efficacy Thesaurus, Application Domain, Technology Topic, Popular Technical Reports.
© 2025 PatSnap. All rights reserved.Legal|Privacy policy|Modern Slavery Act Transparency Statement|Sitemap|About US| Contact US: help@patsnap.com