Threading sealing structure of ultrasonic transducer
A technology of ultrasonic transducer and sealing structure, which is applied in the sealing of engines, medical science, pipes, etc., can solve the problems of open circuit, not being large enough, conductive metal rings and plastic parts not being well sealed, etc., to improve the safety factor, To ensure the effect of normal transmission
- Summary
- Abstract
- Description
- Claims
- Application Information
AI Technical Summary
Problems solved by technology
Method used
Image
Examples
Embodiment Construction
[0021] In order to enable those skilled in the art to better understand the technical solutions of the present invention, the present invention will be further described in detail below in conjunction with the accompanying drawings and preferred embodiments.
[0022] As shown in the figure, the present invention includes a transducer housing 1, a conductive ring assembly 2, a threading sealing assembly 3, a manual control wire 4 and a transducer clamping assembly 5, and the transducer housing 1 includes at least a first segment housing 11 and the second segment housing 12 , the conductive ring assembly 2 includes an outer conductive ring 21 , an insulator 22 and an inner conductive ring 23 . The outer conductive ring 21 and the inner conductive ring 23 transmit manual control signals, and the insulator 22 isolates and insulates the outer conductive ring 21 and the inner conductive ring 23 . The threading seal assembly 3 includes a front flexible seal 31, a rigid support body 3...
PUM
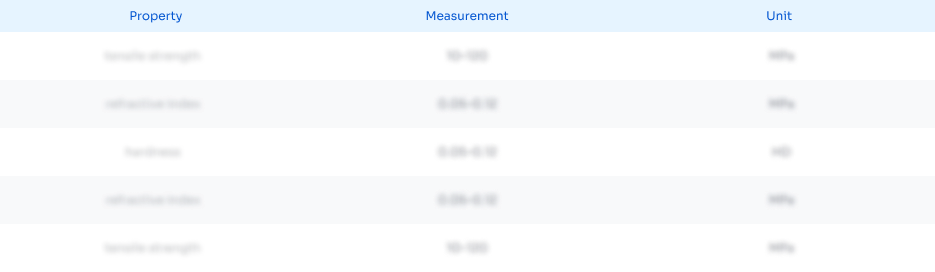
Abstract
Description
Claims
Application Information

- R&D
- Intellectual Property
- Life Sciences
- Materials
- Tech Scout
- Unparalleled Data Quality
- Higher Quality Content
- 60% Fewer Hallucinations
Browse by: Latest US Patents, China's latest patents, Technical Efficacy Thesaurus, Application Domain, Technology Topic, Popular Technical Reports.
© 2025 PatSnap. All rights reserved.Legal|Privacy policy|Modern Slavery Act Transparency Statement|Sitemap|About US| Contact US: help@patsnap.com