Method for controlling ultralow emission of sintering flue gas
A sintering flue gas, ultra-low technology, applied in the steam generation method, separation method, chemical instrument and method using heat carrier, etc., can solve the problem of large investment cost and operating cost, high cost, large investment in activated carbon desulfurization and denitrification operation, etc. problems, to achieve the effect of reducing system cost, increasing waste heat power generation, and improving application prospects
- Summary
- Abstract
- Description
- Claims
- Application Information
AI Technical Summary
Problems solved by technology
Method used
Image
Examples
Embodiment approach 1
[0028] Embodiment 1 The sintering fan of a 380m2 sintering machine is 2×1.2 million m3 / h, the utilization factor is 1.23t / m2·h, the fan with cooling machine is 7×260,000 m3 / h, the thickness of the material layer is 900mm, and the temperature of the bellows of the sintering machine is as follows The bellows under each trolley are double-row bellows (south side, north side), and there is a bellows branch pipe under each bellows box to connect the large flue to double flue, and double fans are arranged. The recyclable heat air box is the first 3 belt cooler fans, and the average temperature of the waste heat power generation system is 385°C. The average emission concentration of SO2 and NOX in the sintering flue gas is 228mg / Nm3 and 180mg / Nm3 respectively, (the current standard of SO2 and NOX is 300mg / Nm3 and 200mg / Nm3), the power generation per ton of ore in the early stage is 10.71kWh / t ore, without the denitrification system, only the desulfurization cost is 10 yuan / t ore.
[...
Embodiment approach 2
[0032]Embodiment 2 A 2×435m2 sintering machine, the main exhaust fan of a single sintering machine is 2×1.5 million m3 / h, the utilization coefficient is 1.3t / m2·h, the fan with cooling machine is 5×420,000 m3 / h, the sintering machine There are 26 bellows, the average temperature of the first 17 bellows is 85°C, and the average temperature of the last 9 bellows is 325°C. The cost of a sintering machine using activated carbon for desulfurization and denitrification is 19.8 yuan / t ore. 360℃, waste heat power generation is 9.6kWh / t mine. The other sintering machine adopts this technology. The cooling of the sintering zone requires an air volume of 2.2 million m3 / h, and the low-temperature sintering flue gas volume is 1.96 million m3 / h, which requires 240,000 m3 / h of air for cooling. The first four are equipped with cooling fans to generate electricity , the intake temperature is 340°C, the waste heat power generation is 16.2kWh / t mine, and the electricity price is 0.5 yuan / kWh, th...
PUM
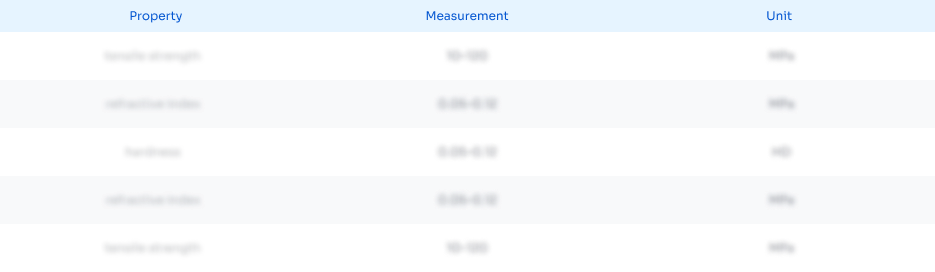
Abstract
Description
Claims
Application Information

- R&D
- Intellectual Property
- Life Sciences
- Materials
- Tech Scout
- Unparalleled Data Quality
- Higher Quality Content
- 60% Fewer Hallucinations
Browse by: Latest US Patents, China's latest patents, Technical Efficacy Thesaurus, Application Domain, Technology Topic, Popular Technical Reports.
© 2025 PatSnap. All rights reserved.Legal|Privacy policy|Modern Slavery Act Transparency Statement|Sitemap|About US| Contact US: help@patsnap.com