High-pressure drive-in quick heating type electric boiler host machine and manufacturing process thereof
A manufacturing process and technology for electric boilers, applied in steam boilers, steam boiler accessories, components of steam boilers, etc. The effect of high efficiency, high practical value and unique novelty
- Summary
- Abstract
- Description
- Claims
- Application Information
AI Technical Summary
Problems solved by technology
Method used
Image
Examples
Embodiment Construction
[0013] The preferred embodiments of the present invention will be described in detail below in conjunction with the accompanying drawings, so that the advantages and features of the present invention can be more easily understood by those skilled in the art, so as to define the protection scope of the present invention more clearly.
[0014] see Figure 1 to Figure 7 , the present invention's high-pressure direct-in rapid heating electric boiler host and its manufacturing process are composed of heating electrical components, heat exchange integrated modules, brackets (2), and pipe fittings; the heating electrical components are composed of heating tubes (14), terminal blocks (13), The terminal connection wire (12), the heating tube support sleeve (15), and the insulating cover (8); the heat exchange integrated module consists of heat exchange profiles (5), profile headers (4), header plugs (9), screws 7), composed of channel steel (10) and screw nut (6); the two ends of N hea...
PUM
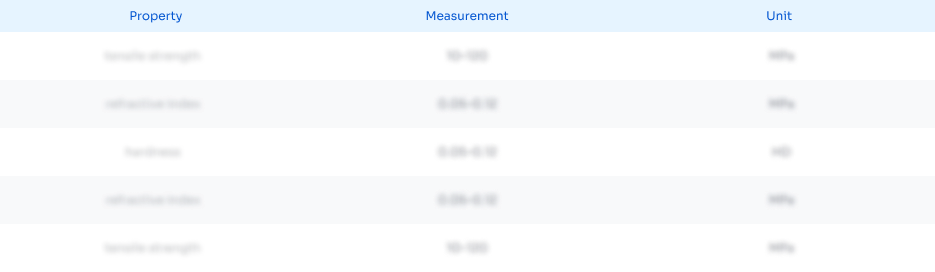
Abstract
Description
Claims
Application Information

- R&D Engineer
- R&D Manager
- IP Professional
- Industry Leading Data Capabilities
- Powerful AI technology
- Patent DNA Extraction
Browse by: Latest US Patents, China's latest patents, Technical Efficacy Thesaurus, Application Domain, Technology Topic, Popular Technical Reports.
© 2024 PatSnap. All rights reserved.Legal|Privacy policy|Modern Slavery Act Transparency Statement|Sitemap|About US| Contact US: help@patsnap.com