Construction method for reducing thickness of aluminum formwork wall
A construction method and technology of aluminum formwork, applied in the direction of formwork/formwork/work frame, connectors of formwork/formwork/work frame, formwork/formwork components, etc., can solve the problem of reduced construction efficiency, low construction efficiency, and poor operation Difficulty and other problems, to achieve the effect of improving production efficiency and processing efficiency, improving construction efficiency, and reducing operation difficulty
- Summary
- Abstract
- Description
- Claims
- Application Information
AI Technical Summary
Problems solved by technology
Method used
Image
Examples
Embodiment Construction
[0026] In order to make the technical problems, technical solutions and beneficial effects to be solved by the present invention clearer, the present invention will be further described in detail below in conjunction with the accompanying drawings and embodiments. It should be understood that the specific embodiments described here are only used to explain the present invention, not to limit the present invention.
[0027] A construction method and structure for reducing the thickness of an aluminum formwork wall, comprising the following steps: designing an aluminum alloy profile mosaic strip 4 equivalent to the amount of thinning on one side of the wall according to the thickness modulus of the construction building wall; according to national and industry standards It is stipulated that the aluminum alloy profile inlaid strip 4 is processed to meet the requirements of the pin hole 41 and the tab groove 42; the aluminum alloy profile inlaid strip 4 and the inner corner formwo...
PUM
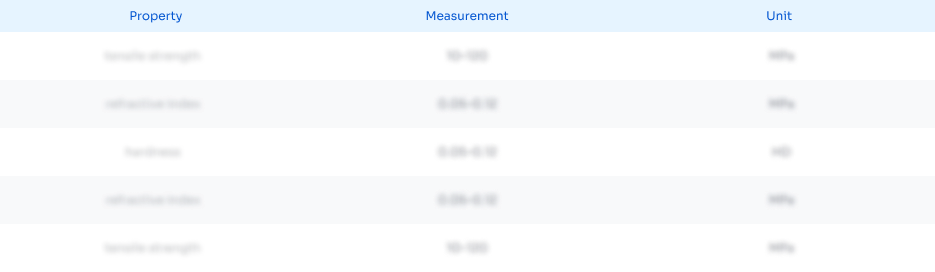
Abstract
Description
Claims
Application Information

- Generate Ideas
- Intellectual Property
- Life Sciences
- Materials
- Tech Scout
- Unparalleled Data Quality
- Higher Quality Content
- 60% Fewer Hallucinations
Browse by: Latest US Patents, China's latest patents, Technical Efficacy Thesaurus, Application Domain, Technology Topic, Popular Technical Reports.
© 2025 PatSnap. All rights reserved.Legal|Privacy policy|Modern Slavery Act Transparency Statement|Sitemap|About US| Contact US: help@patsnap.com