Method for machining bottle-shaped shaft of large pumped storage generator motor
A technology for generating electric motors and pumped water storage, which is applied to the rotating parts of the magnetic circuit, the shape/style/structure of the magnetic circuit, etc., which can solve the problems of affecting the processing accuracy and increasing the processing difficulty, so as to meet the requirements of high precision and improve the processing accuracy , the effect of reducing the error
- Summary
- Abstract
- Description
- Claims
- Application Information
AI Technical Summary
Problems solved by technology
Method used
Image
Examples
Embodiment 1
[0034] see Figure 1-Figure 3 , a method for processing a bottle-shaped shaft of a large-scale pumped-storage generator motor, comprising the following steps:
[0035] a. Install the end face of the big end of the bottle-shaped shaft on the boring machine on the working platform, and bore the matching hole between the center of the big end and the transition connecting plate 7;
[0036] b. Turning the outer circle of the transition connecting plate 7 and the welding groove, installing and welding the transition connecting plate 7 into the center hole of the big end of the bottle shaft, boring and processing the transition connecting plate 7 and the process dummy shaft to coordinate the positioning seam and transition connection Plate 7 flange joint screw holes and positioning pin 9 holes;
[0037] c. The flange joint hole and locating pin 9 holes of the flange matching the dummy shaft of the boring process and the transition connecting plate 7, install the dummy shaft of the ...
Embodiment 2
[0042] see Figure 1-Figure 3 , a method for processing a bottle-shaped shaft of a large-scale pumped-storage generator motor, comprising the following steps:
[0043] a. Install the end face of the big end of the bottle-shaped shaft on the boring machine on the working platform, and bore the matching hole between the center of the big end and the transition connecting plate 7;
[0044] b. Turning the outer circle of the transition connecting plate 7 and the welding groove, installing and welding the transition connecting plate 7 into the center hole of the big end of the bottle shaft, boring and processing the transition connecting plate 7 and the process dummy shaft to coordinate the positioning seam and transition connection Plate 7 flange joint screw holes and positioning pin 9 holes;
[0045] c. The flange joint hole and locating pin 9 holes of the flange matching the dummy shaft of the boring process and the transition connecting plate 7, install the dummy shaft of the ...
Embodiment 3
[0051] see Figure 1-Figure 3 , a method for processing a bottle-shaped shaft of a large-scale pumped-storage generator motor, comprising the following steps:
[0052] a. Install the end face of the big end of the bottle-shaped shaft on the boring machine on the working platform, and bore the matching hole between the center of the big end and the transition connecting plate 7;
[0053] b. Turning the outer circle of the transition connecting plate 7 and the welding groove, installing and welding the transition connecting plate 7 into the center hole of the big end of the bottle shaft, boring and processing the transition connecting plate 7 and the process dummy shaft to coordinate the positioning seam and transition connection Plate 7 flange joint screw holes and positioning pin 9 holes;
[0054] c. The flange joint hole and locating pin 9 holes of the flange matching the dummy shaft of the boring process and the transition connecting plate 7, install the dummy shaft of the ...
PUM
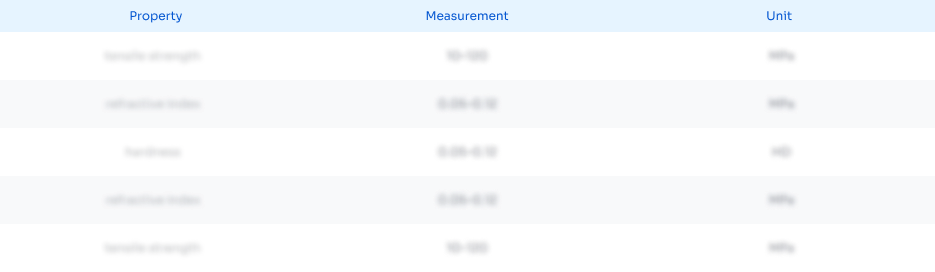
Abstract
Description
Claims
Application Information

- Generate Ideas
- Intellectual Property
- Life Sciences
- Materials
- Tech Scout
- Unparalleled Data Quality
- Higher Quality Content
- 60% Fewer Hallucinations
Browse by: Latest US Patents, China's latest patents, Technical Efficacy Thesaurus, Application Domain, Technology Topic, Popular Technical Reports.
© 2025 PatSnap. All rights reserved.Legal|Privacy policy|Modern Slavery Act Transparency Statement|Sitemap|About US| Contact US: help@patsnap.com