Stamping die for metal product casting
A technology for stamping dies and metal products, applied in the field of dies, can solve problems such as affecting the structural strength of the dies, deteriorating the working environment by noise, etc.
- Summary
- Abstract
- Description
- Claims
- Application Information
AI Technical Summary
Problems solved by technology
Method used
Image
Examples
Embodiment 1
[0024] see figure 1 , the present invention provides a stamping die for metal product casting, its structure includes: upper die base 1, ejector punch 2, convex plate 3, spring plunger 4, said upper die base 1 is provided with ejector punch 2. The top position of the ejector punch 2 corresponds to the convex plate 3, the side of the convex plate 3 is connected to the spring plunger 4, and the upper mold base 1 is the main structure of the mold equipment. On the one hand, it plays the role of building the basic shape of the structure and carrying other The role of components, on the other hand, is used to protect the internal components in the process of stamping and manufacturing metal products. The ejector punch 2 is the core operating structure of the mold, and the convex plate 3 on the top is used The transformation of its displacement changes to shape the shape of the metal raw material to meet the production requirements. The spring plunger 4 is used to support the stabi...
Embodiment 2
[0031] The description of the second embodiment drawn in conjunction with the first embodiment, combined with image 3 , Figure 4 and Figure 5 , the sides of the presser 13 are annularly equidistantly provided with isolation side pins 14, and the bottom of the rack 18 is provided with rebound layers 19 at intervals, and the rebound layers 19 and the sponge hole layer 20 are both arranged on the vertical block 21 of the machine tool , the vertical blocks 21 of the machine tool are connected by corrugated bars 22, and a stress wheel 26 is provided on one side of the spacer 25 and is connected to it. Magnetic rod 28, when the mold is stamping and manufacturing metal products, due to the different processing contents of each process, the pressure required for the press 13 to press the workpiece is also different, and the greater the pressure of the press 13, the greater the reaction force released , the reaction force acts on the presser 13, and the noise generated by the inst...
PUM
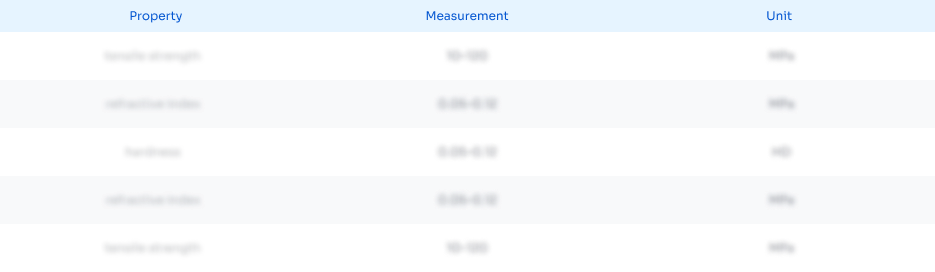
Abstract
Description
Claims
Application Information

- R&D
- Intellectual Property
- Life Sciences
- Materials
- Tech Scout
- Unparalleled Data Quality
- Higher Quality Content
- 60% Fewer Hallucinations
Browse by: Latest US Patents, China's latest patents, Technical Efficacy Thesaurus, Application Domain, Technology Topic, Popular Technical Reports.
© 2025 PatSnap. All rights reserved.Legal|Privacy policy|Modern Slavery Act Transparency Statement|Sitemap|About US| Contact US: help@patsnap.com