Method for determining gap between auxiliary shoulders of double-shoulder drill pipe joint
A drill pipe joint and determination method technology, applied in the direction of drill pipe, drill pipe, drilling equipment, etc., can solve the problems of oilfield economic loss, double shoulder drill pipe joint failure, and limit the performance of double shoulder drill pipe joint, etc., to achieve Significant technical progress and the effect of highlighting substantive features
- Summary
- Abstract
- Description
- Claims
- Application Information
AI Technical Summary
Problems solved by technology
Method used
Image
Examples
Embodiment Construction
[0027] The present invention will be further described below in conjunction with the accompanying drawings and embodiments.
[0028] see figure 1 , a method for determining the secondary shoulder clearance of a double-shoulder drill pipe joint, according to the combined action of make-up torque, axial tension, bending moment, and working torque external loads of double-shoulder drill pipe joints with different secondary shoulder clearance characteristics Based on the stress characteristics of the three-dimensional elastoplastic finite element calculation, the optimal secondary shoulder clearance for this type of double-shoulder drill pipe joint suitable for a specific operating well depth is determined, including the following steps:
[0029] 1) Use special tools to measure the geometric parameters of the double-shoulder drill pipe joint, including joint outer diameter, inner diameter, thread tooth parameters, box bore, pin nose, shoulder parameters;
[0030] 2) Use the mater...
PUM
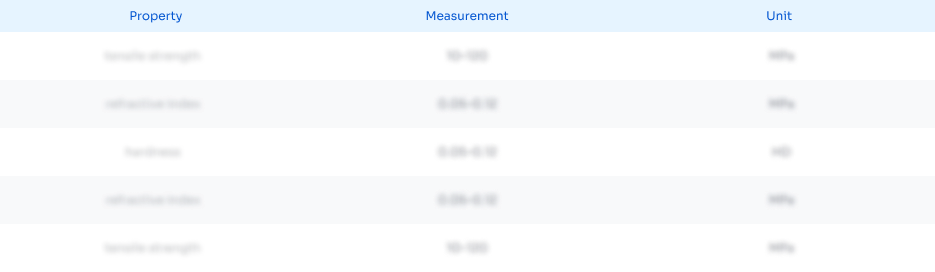
Abstract
Description
Claims
Application Information

- R&D Engineer
- R&D Manager
- IP Professional
- Industry Leading Data Capabilities
- Powerful AI technology
- Patent DNA Extraction
Browse by: Latest US Patents, China's latest patents, Technical Efficacy Thesaurus, Application Domain, Technology Topic, Popular Technical Reports.
© 2024 PatSnap. All rights reserved.Legal|Privacy policy|Modern Slavery Act Transparency Statement|Sitemap|About US| Contact US: help@patsnap.com