Laser vision positioning correction method for cutting complex workpiece by robot
A technology for complex workpieces and robots, which is applied to manipulators, manufacturing tools, metal processing equipment, etc., and can solve problems such as defective products and workpiece cutting
- Summary
- Abstract
- Description
- Claims
- Application Information
AI Technical Summary
Problems solved by technology
Method used
Image
Examples
Embodiment Construction
[0033] The following will clearly and completely describe the technical solutions in the embodiments of the present invention with reference to the accompanying drawings in the embodiments of the present invention. Obviously, the described embodiments are only some, not all, embodiments of the present invention. Based on the embodiments of the present invention, all other embodiments obtained by persons of ordinary skill in the art without making creative efforts belong to the protection scope of the present invention.
[0034] see Figure 1-3 , an embodiment of the present invention provides a technical solution: a laser vision positioning correction method for cutting complex workpieces by robots, comprising the following steps:
[0035] Step 1. Coordinate system change: switch the robot coordinate system to the world coordinate system;
[0036] Step 2. Preliminary coordinate confirmation: Try to teach the three scanning positions of the laser vision sensor on the inner cir...
PUM
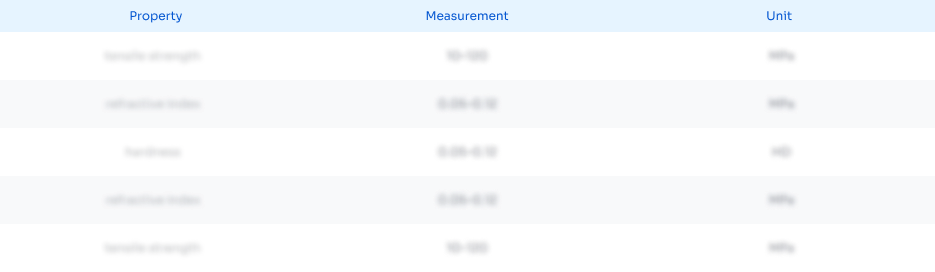
Abstract
Description
Claims
Application Information

- R&D Engineer
- R&D Manager
- IP Professional
- Industry Leading Data Capabilities
- Powerful AI technology
- Patent DNA Extraction
Browse by: Latest US Patents, China's latest patents, Technical Efficacy Thesaurus, Application Domain, Technology Topic, Popular Technical Reports.
© 2024 PatSnap. All rights reserved.Legal|Privacy policy|Modern Slavery Act Transparency Statement|Sitemap|About US| Contact US: help@patsnap.com