Machining process of normally-engaged gear
A processing technology and constant meshing technology, which is applied in the field of constant meshing gear processing technology, can solve the problems of no obvious improvement in gear grinding accuracy, reduced wear resistance of end faces, and increased costs.
- Summary
- Abstract
- Description
- Claims
- Application Information
AI Technical Summary
Problems solved by technology
Method used
Image
Examples
Embodiment Construction
[0020] The implementation of the present invention will be described in more detail below with reference to the accompanying drawings and reference numerals, so that those skilled in the art can implement it after studying this specification. It should be understood that the specific embodiments described here are only used to explain the present invention, not to limit the present invention.
[0021] The invention provides a constant mesh gear processing technology, including the following steps:
[0022] Process 1, embryo making, using hot die forging to forge the tooth embryo of the gear;
[0023] Process 2, pulling the spline, broaching the inner spline hole on the tooth blank, and controlling the runout tolerance of the end face of the gear;
[0024] Process 3, gear hobbing, the gear teeth are processed by the hob;
[0025] Process 4, chamfering, the sharp corner on the tooth profile of the inverted cogwheel tooth;
[0026] Step 5, heat treatment, put the gear into the...
PUM
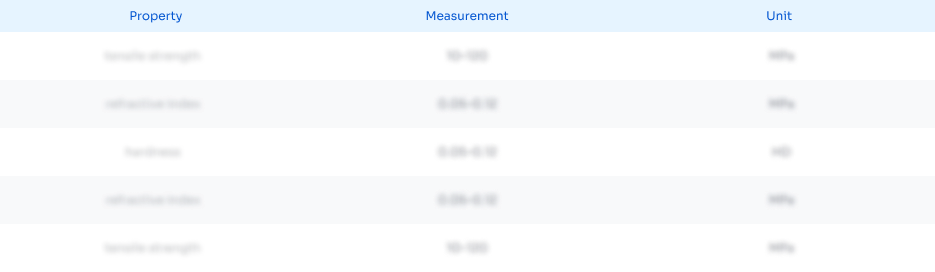
Abstract
Description
Claims
Application Information

- R&D Engineer
- R&D Manager
- IP Professional
- Industry Leading Data Capabilities
- Powerful AI technology
- Patent DNA Extraction
Browse by: Latest US Patents, China's latest patents, Technical Efficacy Thesaurus, Application Domain, Technology Topic, Popular Technical Reports.
© 2024 PatSnap. All rights reserved.Legal|Privacy policy|Modern Slavery Act Transparency Statement|Sitemap|About US| Contact US: help@patsnap.com