Method for preparing antistatic black master batch from graphene-coated carbon black, and product
A technology for alkene-coated carbon black and black masterbatch, applied in the field of preparation of carbon black colored masterbatch, can solve the problems of difficult dispersion of polymer matrix, substandard antistatic performance, low concentration of black masterbatch, etc. Electrostatic properties, excellent antistatic properties, the effect of improving product stability
- Summary
- Abstract
- Description
- Claims
- Application Information
AI Technical Summary
Problems solved by technology
Method used
Image
Examples
Embodiment 1
[0056] First, 1g sodium lauryl sulfate (the mass ratio of carbon black to sodium lauryl sulfate is 40:1), select CSX-941 carbon black and ethanol (the mass ratio of carbon black to ethanol is 1:1) Stir evenly at 60°C, obtain a modified carbon black dispersion after mixing and react, and obtain modified carbon black after drying; then disperse graphene oxide and modified carbon black in 100ml water respectively (graphene oxide and modified carbon black The mass ratio of carbon black is 1:50), and the graphene oxide aqueous solution is added to the modified carbon black aqueous solution, and stirred evenly to obtain a graphene oxide-coated carbon black dispersion; finally, the prepared graphene oxide-coated carbon After the black dispersion is centrifuged, washed and dried, the graphene oxide-coated carbon black is obtained. Figure 1a Be the optical micrograph of the graphene oxide coated carbon black dispersion liquid prepared in embodiment 1; Figure 1b It is the SEM figure ...
Embodiment 2
[0060] First mix 1g of DL-602 (the mass ratio of carbon black to DL-602 is 40:1), select CSX-941 carbon black and ethanol (the mass ratio of carbon black to ethanol is 1:1) and stir evenly at 60°C , obtain modified carbon black dispersion liquid after mixing reaction, get modified carbon black after drying; Then graphene oxide and modified carbon black are respectively dispersed in 100ml water (the quality of graphene oxide and modified carbon black Ratio 1:50), adding the graphene oxide aqueous solution into the modified carbon black aqueous solution, stirring evenly to obtain a graphene oxide-coated carbon black dispersion; finally the prepared graphene oxide-coated carbon black dispersion was centrifuged and washed After drying, graphene oxide-coated carbon black is obtained. Add 1 g of graphene oxide-coated modified carbon black to 100 ml of deionized water for ultrasonic dispersion, add reducing agent ascorbic acid, and react at 60° C. for 1 h (the mass ratio of graphene ...
Embodiment 3
[0063] First mix 1g APS with DL-602 (the mass ratio of carbon black to DL-602 is 40:1; the mass ratio of APS to DL-602 is 1:1), select CSX-941 carbon black and ethanol (carbon black and ethanol The mass ratio is 1:5) Stir evenly at 60°C, get modified carbon black dispersion liquid after mixing and reaction, and get modified carbon black after drying; then disperse graphene oxide and modified carbon black separately In 100ml of water (the mass ratio of graphene oxide and modified carbon black is 1:70), the graphene oxide aqueous solution is added in the modified carbon black aqueous solution, stir well, obtain graphene oxide coating carbon black dispersion liquid; Finally After the prepared graphene oxide-coated carbon black dispersion is centrifuged, washed and dried, the graphene oxide-coated carbon black is obtained. Add 1 g of graphene oxide-coated modified carbon black to 100 ml of deionized water for ultrasonic dispersion, add reducing agent ascorbic acid, and react at 60...
PUM
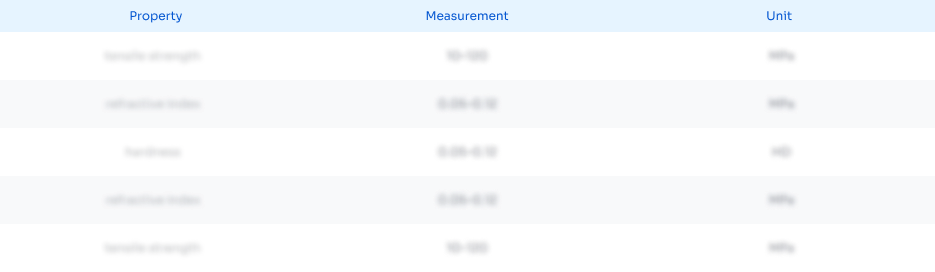
Abstract
Description
Claims
Application Information

- R&D
- Intellectual Property
- Life Sciences
- Materials
- Tech Scout
- Unparalleled Data Quality
- Higher Quality Content
- 60% Fewer Hallucinations
Browse by: Latest US Patents, China's latest patents, Technical Efficacy Thesaurus, Application Domain, Technology Topic, Popular Technical Reports.
© 2025 PatSnap. All rights reserved.Legal|Privacy policy|Modern Slavery Act Transparency Statement|Sitemap|About US| Contact US: help@patsnap.com