Method for improving Bs of MnZn power ferrite material by moving valley point
A ferrite material and power technology, applied in the manufacture of inductors/transformers/magnets, electrical components, circuits, etc., can solve the problem of increased material loss, and achieve the effect of reducing loss, reducing high temperature loss, and improving Bs
- Summary
- Abstract
- Description
- Claims
- Application Information
AI Technical Summary
Problems solved by technology
Method used
Image
Examples
Embodiment 1
[0024] Embodiment 1: a kind of method that moves valley point and improves MnZn power ferrite material Bs, comprises the following steps:
[0025] 1) 52.9mol% Fe 2 o 3 , 38.3mol% of MnO and 8.8mol% of ZnO are mixed, and the next sanding time is 1.5h at the material ball water ratio of 1:5:0.4;
[0026] 2) adding 10% of the total mass of the calcined material and glue with a mass fraction of 7.5%, spraying and granulating, and then pre-calcining at 900°C in a rotary kiln to obtain the calcined material;
[0027] 3) Add additives comprising the following components in the calcined material and account for the mass percentage of the calcined material: CaCO 3 0.03%, ZrO 2 0.04%, Co 2 o 3 0.44%, SnO 2 0.05%, followed by secondary sanding for 1.5h under the ratio of ball water to 1:5:0.4;
[0028]4) Add glue with a total mass of 10% of the secondary abrasive and a mass fraction of 7.5% to the secondary abrasive, spray and granulate, press at 6Mpa to form a standard ring, and ...
Embodiment 2
[0029] Embodiment 2: a kind of method that moves valley point and improves MnZn power ferrite material Bs, comprises the following steps:
[0030] 1) 53.3mol% Fe 2 o 3 , 39.08mol% of MnO and 7.62mol% of ZnO are mixed, and the water ratio of the material ball is 1:7:0.6 for the next sanding for 0.5h;
[0031] 2) adding 10% of the total mass of the calcined material and glue with a mass fraction of 7.5%, spraying and granulating, and then pre-calcining at 1000°C in a rotary kiln to obtain the calcined material;
[0032] 3) Add additives comprising the following components in the calcined material and account for the mass percentage of the calcined material: CaCO 3 0.03%, ZrO 2 0.04%, Co 2 o 3 0.48%, SnO 2 0.05%, followed by secondary sanding for 0.5h at the ratio of ball water to 1:7:0.6;
[0033] 4) Add glue with a total mass of 10% of the secondary abrasive and a mass fraction of 7.5% to the secondary abrasive, spray and granulate, press at 8Mpa to form a standard ring,...
Embodiment 3
[0034] Embodiment 3: a kind of method that moves valley point and improves MnZn power ferrite material Bs, comprises the following steps:
[0035] 1) 53.1mol% Fe 2 o 3 , 38.5 mol% of MnO and 8.4 mol% of ZnO are mixed, and the next sanding time is 1h at the material ball water ratio of 1:6:0.5;
[0036] 2) adding 10% of the total mass of the calcined material and glue with a mass fraction of 7.5%, spraying and granulating, and then pre-calcining at 950°C in a rotary kiln to obtain the calcined material;
[0037] 3) Add additives comprising the following components in the calcined material and account for the mass percentage of the calcined material: CaCO 3 0.03%, ZrO 2 0.04%, Co 2 o 3 0.52%, SnO 2 0.05%, followed by secondary sanding for 1h at the ratio of ball water to 1:6:0.5;
[0038] 4) Add glue with a total mass of 10% of the secondary abrasive and a mass fraction of 7.5% to the secondary abrasive, spray and granulate, press at 7Mpa to form a standard ring, and then...
PUM
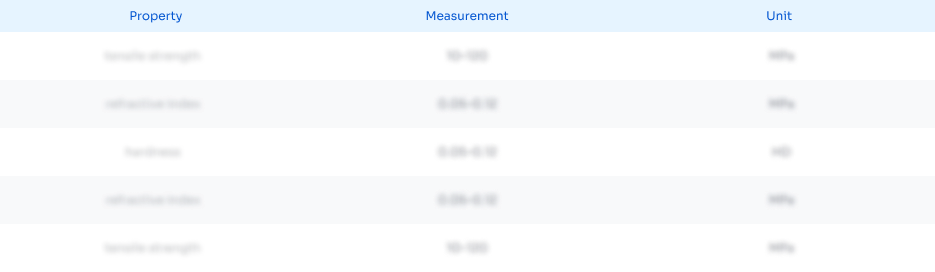
Abstract
Description
Claims
Application Information

- R&D
- Intellectual Property
- Life Sciences
- Materials
- Tech Scout
- Unparalleled Data Quality
- Higher Quality Content
- 60% Fewer Hallucinations
Browse by: Latest US Patents, China's latest patents, Technical Efficacy Thesaurus, Application Domain, Technology Topic, Popular Technical Reports.
© 2025 PatSnap. All rights reserved.Legal|Privacy policy|Modern Slavery Act Transparency Statement|Sitemap|About US| Contact US: help@patsnap.com