Premixing treatment method for ink production and preparation
A processing method and pre-mixing technology, applied in mixers, chemical instruments and methods, chemical/physical processes, etc., can solve the problems of large resistance of mixing blades, damage of mixing blades, and difficulty in ensuring the contact of mixers, and reduce work intensity, The effect of reducing workload and ensuring sufficiency
- Summary
- Abstract
- Description
- Claims
- Application Information
AI Technical Summary
Problems solved by technology
Method used
Image
Examples
Embodiment Construction
[0036] The embodiments of the present invention will be described in detail below with reference to the accompanying drawings, but the present invention can be implemented in many different ways defined and covered by the claims.
[0037] Such as Figure 1 to Figure 7 As shown, a pre-mixing treatment method for ink production and preparation, which uses an automatic mixing device, the automatic mixing device includes a stirring tank 1, a stirring mechanism 2 and a feeding mechanism 3, and the specific method when using the above-mentioned automatic mixing device to make ink The process is as follows:
[0038] S1. Material ratio: manually weigh the corresponding weight of the material according to the ratio;
[0039] S2. Initial feeding: manually put part of the prepared materials into the mixing tank 1;
[0040] S3. Stirring: the material in the mixing tank 1 is stirred by the stirring mechanism 2, so that the material can be mixed evenly;
[0041] S4. Feeding again: add ma...
PUM
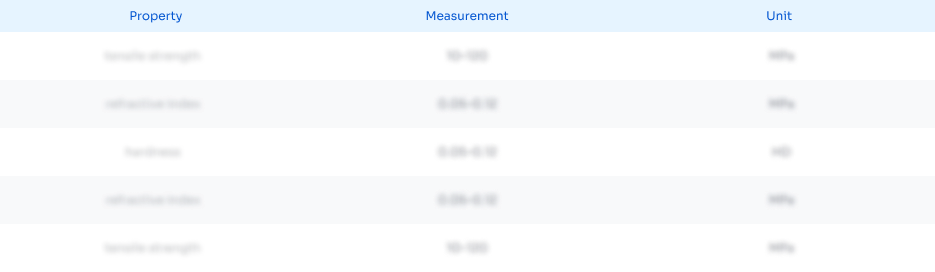
Abstract
Description
Claims
Application Information

- Generate Ideas
- Intellectual Property
- Life Sciences
- Materials
- Tech Scout
- Unparalleled Data Quality
- Higher Quality Content
- 60% Fewer Hallucinations
Browse by: Latest US Patents, China's latest patents, Technical Efficacy Thesaurus, Application Domain, Technology Topic, Popular Technical Reports.
© 2025 PatSnap. All rights reserved.Legal|Privacy policy|Modern Slavery Act Transparency Statement|Sitemap|About US| Contact US: help@patsnap.com