Wind turbine blade aerodynamic structure coupling design method
A technique for coupling design, wind turbine blades
- Summary
- Abstract
- Description
- Claims
- Application Information
AI Technical Summary
Problems solved by technology
Method used
Image
Examples
Embodiment Construction
[0044] The present invention will be further described below in conjunction with specific examples.
[0045] The specific conditions of the coupling design method for the aerodynamic structure of wind power blades provided in this embodiment are as follows:
[0046] 1) Input design parameters
[0047] Unit-related parameters: input unit rated power, maximum speed, unit loss, average wind speed, Weibull distribution curve shape parameter k, axial thrust limit value, maximum allowable waving deformation, wind energy utilization coefficient Cp design value.
[0048] Geometric design parameters: maximum chord length change range and change step size, blade root chord length change range and change step size, spanwise position range and change step size corresponding to the maximum chord length, chord length range and change step size near the blade tip Length, thickness design parameters, root to tip spar layup function distribution.
[0049] 2) Blade geometric parameter design
...
PUM
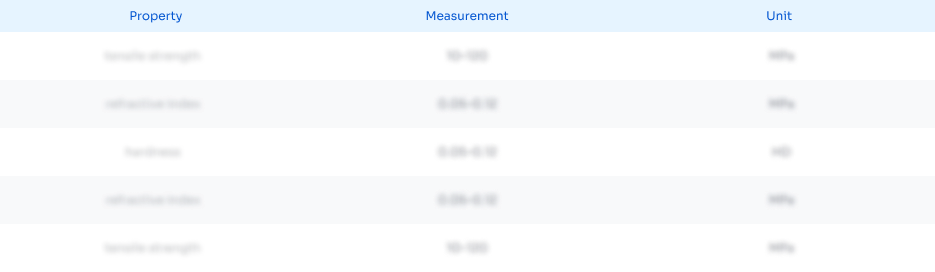
Abstract
Description
Claims
Application Information

- R&D
- Intellectual Property
- Life Sciences
- Materials
- Tech Scout
- Unparalleled Data Quality
- Higher Quality Content
- 60% Fewer Hallucinations
Browse by: Latest US Patents, China's latest patents, Technical Efficacy Thesaurus, Application Domain, Technology Topic, Popular Technical Reports.
© 2025 PatSnap. All rights reserved.Legal|Privacy policy|Modern Slavery Act Transparency Statement|Sitemap|About US| Contact US: help@patsnap.com