A high-precision oil-impregnated bearing sleeve processing equipment and method
A high-precision, bearing technology, used in metal processing equipment, grinding/polishing equipment, manufacturing tools, etc., can solve the problems of time-consuming, labor-intensive, low discharge efficiency and separation efficiency, and expand the scope of application and improve the discharge efficiency. and separation efficiency, the effect of improving separation and discharge efficiency
- Summary
- Abstract
- Description
- Claims
- Application Information
AI Technical Summary
Problems solved by technology
Method used
Image
Examples
Embodiment 1
[0048] Embodiment one: refer to figure 1 , is a high-precision oil-impregnated bearing sleeve processing equipment disclosed in the present invention, including a body 1, a vibration seat 12 arranged at the bottom of the body 1, a vibration box 13 arranged at the top of the body 1, and a vibration box 13 arranged between the vibration seat 12 and the vibration box 13. The vibrating mechanism 16 between them and the dispersing mechanism arranged on one side of the vibrating base 12 are used to separate abrasives and workpieces. Vibration box 13 is provided with an annular vibrating cavity 14 for mixing workpieces and abrasives. Vibrating mechanism 16 includes vibrating motor 161 arranged on vibrating base 12. Vibrating motor 161 and vibrating base 12 are fixed by screws. When vibrating motor 161 When starting, the vibrating box 13 is driven to vibrate so that the mixture of the workpiece and abrasive is rotated clockwise or counterclockwise around the vibrating chamber 14 for p...
Embodiment 2
[0061] Embodiment 2: A method for processing a high-precision oil-impregnated bearing sleeve, comprising the following steps:
[0062] S100: according to the size of the bearing sleeve, change the clearance of the sieve rod 31 through the slider 34;
[0063] S200: Put the bearing sleeve and the abrasive into the vibration cavity 14 after being mixed, and switch the channel changing plate 21 to a contact position with the outer wall of the vibration cavity 14;
[0064] S300: Turn on the vibration motor 161, and the vibration motor 161 drives the mixture of the workpiece and the abrasive to rotate clockwise or counterclockwise around the ring-shaped vibration chamber 14 and perform vibration polishing, at this time, the bearing sleeve and the abrasive are in an internal circulation state;
[0065] S400: After polishing, turn the channel changing plate 21 to connect with the central column 131, and the mixture of workpiece and abrasive reaches the discharge port 15 along the chan...
PUM
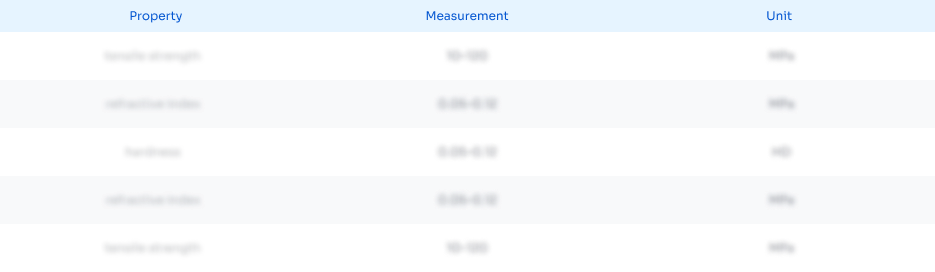
Abstract
Description
Claims
Application Information

- Generate Ideas
- Intellectual Property
- Life Sciences
- Materials
- Tech Scout
- Unparalleled Data Quality
- Higher Quality Content
- 60% Fewer Hallucinations
Browse by: Latest US Patents, China's latest patents, Technical Efficacy Thesaurus, Application Domain, Technology Topic, Popular Technical Reports.
© 2025 PatSnap. All rights reserved.Legal|Privacy policy|Modern Slavery Act Transparency Statement|Sitemap|About US| Contact US: help@patsnap.com