SLM forming method based on intelligent scanning path planning and product
A scanning path, laser scanning path technology, applied in the SLM forming method and product field based on intelligent scanning path planning, can solve the problems of no fundamental change in scanning strategy, unoptimized scanning method, and unchanged scanning method, so as to avoid heat Concentration, avoiding temperature gradient, and improving the effect of forming accuracy
- Summary
- Abstract
- Description
- Claims
- Application Information
AI Technical Summary
Problems solved by technology
Method used
Image
Examples
Embodiment Construction
[0034] In order to make the object, technical solution and advantages of the present invention clearer, the present invention will be further described in detail below in conjunction with the accompanying drawings and embodiments. It should be understood that the specific embodiments described here are only used to explain the present invention, not to limit the present invention. In addition, the technical features involved in the various embodiments of the present invention described below can be combined with each other as long as they do not constitute a conflict with each other.
[0035] Such as figure 1 As shown, a kind of SLM forming method based on intelligent scanning path planning provided by the present invention, its steps are as follows:
[0036] S1, performing layered slicing processing on the part three-dimensional model file (such as an STL format file), that is, cutting it according to a fixed layer thickness, and obtaining the cutting ring profile of each la...
PUM
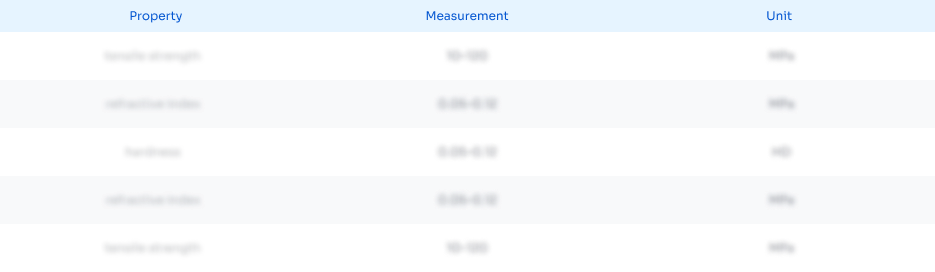
Abstract
Description
Claims
Application Information

- R&D
- Intellectual Property
- Life Sciences
- Materials
- Tech Scout
- Unparalleled Data Quality
- Higher Quality Content
- 60% Fewer Hallucinations
Browse by: Latest US Patents, China's latest patents, Technical Efficacy Thesaurus, Application Domain, Technology Topic, Popular Technical Reports.
© 2025 PatSnap. All rights reserved.Legal|Privacy policy|Modern Slavery Act Transparency Statement|Sitemap|About US| Contact US: help@patsnap.com