A bridge structure for relining manipulator
A bridge structure and manipulator technology, applied in the direction of mechanical conveyors, conveyors, lifting frames, etc., can solve the problem that the height of the lining trolley cannot be satisfied, and achieve the effect of strong practicability
- Summary
- Abstract
- Description
- Claims
- Application Information
AI Technical Summary
Problems solved by technology
Method used
Image
Examples
Embodiment Construction
[0035] The following will clearly and completely describe the technical solutions in the embodiments of the present invention with reference to the accompanying drawings in the embodiments of the present invention. Obviously, the described embodiments are only some, not all, embodiments of the present invention. Based on the embodiments of the present invention, all other embodiments obtained by persons of ordinary skill in the art without creative efforts fall within the protection scope of the present invention.
[0036] see Figure 1-10 As shown, the present invention is a bridge structure for relining manipulators, including an underframe 1, a first slide rail 6 is fixedly installed on both sides of the top of the underframe 1, and a first slide link block 5 is slidably installed on the first slide rail 6 A first connecting shaft 7 is arranged between the two first sliding link blocks 5, and the first connecting shaft 7 is rotatably arranged between the two first sliding l...
PUM
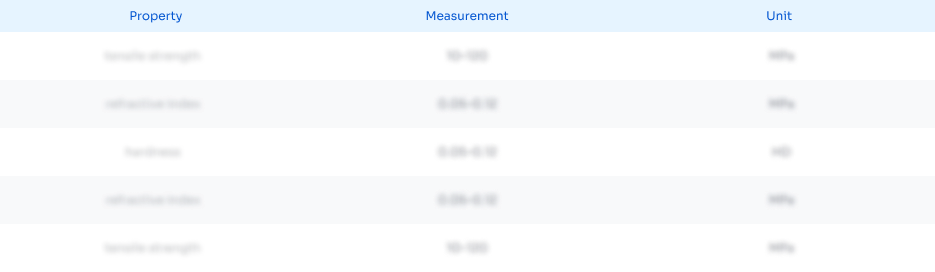
Abstract
Description
Claims
Application Information

- R&D
- Intellectual Property
- Life Sciences
- Materials
- Tech Scout
- Unparalleled Data Quality
- Higher Quality Content
- 60% Fewer Hallucinations
Browse by: Latest US Patents, China's latest patents, Technical Efficacy Thesaurus, Application Domain, Technology Topic, Popular Technical Reports.
© 2025 PatSnap. All rights reserved.Legal|Privacy policy|Modern Slavery Act Transparency Statement|Sitemap|About US| Contact US: help@patsnap.com