Robot touch servo control method for milling of easily-deformed structure
A milling processing and servo control technology, which is applied in the direction of metal processing machinery parts, metal processing, automatic control devices, etc., can solve the problems of easy deformation of the structure, destruction of milling results, displacement, etc., to achieve strong flexibility and prevent mutual interference Effect
- Summary
- Abstract
- Description
- Claims
- Application Information
AI Technical Summary
Problems solved by technology
Method used
Image
Examples
Embodiment 1
[0038] The technical solutions of the present invention are further described in detail below with reference to the accompanying drawings.
[0039] like figure 1 The shown robot tactile servo control system for the milling of deformable structures, the system includes a milling robot equipped with a milling tool, an accelerometer sensor array module, a communication module, a controller, a motor control module and a host computer: the milling The vibration signal is collected by the accelerometer sensor array module and transmitted to the controller by the communication module. The controller executes the control algorithm to generate the result and transmits it to the motor drive module, and then the motor drive module controls the motion of the robot to keep the milling depth unchanged. The controller will also be transmitted to the upper computer, and the upper computer can display the milling status in real time and can send commands to control the operation and stop of th...
PUM
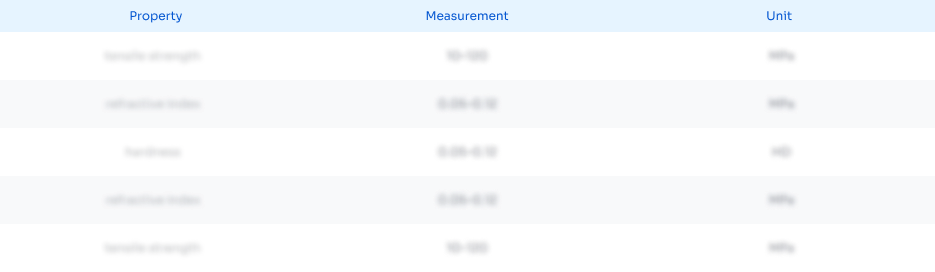
Abstract
Description
Claims
Application Information

- Generate Ideas
- Intellectual Property
- Life Sciences
- Materials
- Tech Scout
- Unparalleled Data Quality
- Higher Quality Content
- 60% Fewer Hallucinations
Browse by: Latest US Patents, China's latest patents, Technical Efficacy Thesaurus, Application Domain, Technology Topic, Popular Technical Reports.
© 2025 PatSnap. All rights reserved.Legal|Privacy policy|Modern Slavery Act Transparency Statement|Sitemap|About US| Contact US: help@patsnap.com