Multi-dimensional force sensor calibration decoupling method based on particle swarm optimization BP neural network
A multi-dimensional force sensor and BP neural network technology, which is applied in the field of multi-dimensional force sensor calibration and decoupling, can solve the problems affecting the measurement accuracy of the sensor, the error of the manufacturing process, and the non-compliance with the measurement requirements, and achieves good convergence and adaptability. Practicality, the effect of good generalization ability
- Summary
- Abstract
- Description
- Claims
- Application Information
AI Technical Summary
Problems solved by technology
Method used
Image
Examples
Embodiment Construction
[0038] Below in conjunction with accompanying drawing and specific embodiment the present invention is described in further detail:
[0039] The present invention provides a multi-dimensional force sensor calibration and decoupling method based on particle swarm optimization BP neural network, optimizes BP network by using PSO (particle swarm algorithm) global search optimal characteristics, and avoids BP algorithm from falling into local optimum during learning To capture the mapping relationship of the calibration data of the conversion channel, the decoupling model has good convergence and adaptability, and the multi-dimensional force sensor has better measurement accuracy.
[0040] As an embodiment of the present invention, such as figure 1 with 2 The six-dimensional force / torque sensor is shown as an example, and the specific embodiments are as follows;
[0041] Firstly, the calibration data of the multi-dimensional force sensor is collected;
[0042] Taking the six-di...
PUM
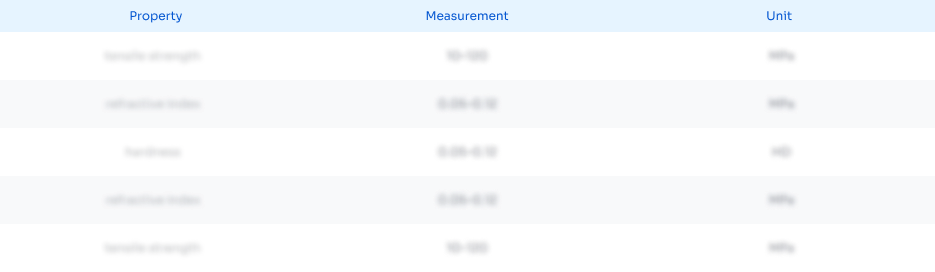
Abstract
Description
Claims
Application Information

- R&D Engineer
- R&D Manager
- IP Professional
- Industry Leading Data Capabilities
- Powerful AI technology
- Patent DNA Extraction
Browse by: Latest US Patents, China's latest patents, Technical Efficacy Thesaurus, Application Domain, Technology Topic, Popular Technical Reports.
© 2024 PatSnap. All rights reserved.Legal|Privacy policy|Modern Slavery Act Transparency Statement|Sitemap|About US| Contact US: help@patsnap.com