Dynamic performance testing system for basic braking device
A basic braking device, dynamic performance technology, applied in braking safety systems, brakes, braking components, etc., can solve problems such as differences in real transmission efficiency
- Summary
- Abstract
- Description
- Claims
- Application Information
AI Technical Summary
Problems solved by technology
Method used
Image
Examples
Embodiment 1
[0077] Such as Figure 10 As shown, the connecting assembly 62 may include a connecting rod 621 for connecting two opposite brake shoe assemblies 61, so as to ensure that each brake shoe assembly 61 can reliably brake the wheel surface of the wheel 42, and the two sides of the connecting rod 621 can also be Mounting seat 622 is provided, and brake shoe assembly 61 can be connected with mounting seat 622 through a suspender. The number of brake cylinders 51 can be two, and the two brake cylinders 51 interact with the two brake shoe assemblies 61 through connecting rods 621 respectively.
[0078] In this embodiment, a second sensor 512 may also be included, installed on the piston rod 511 of the brake cylinder 51, for monitoring the single-rod thrust of the piston rod 511, by comparing the single-rod thrust with that measured by the first sensor 56 The actual measured braking force can be used to calibrate the relationship between the single-rod thrust and the measured braking f...
Embodiment 2
[0080] Such as Figure 11 As shown, the connection assembly 62 may include a brake beam 623 and two mounting seats 622 opposite to each other. The brake beam 623 is used to connect the two opposite brake shoe assemblies 61, and the two ends of the brake beam 623 are respectively connected to the two sides. The mounting seat 622 forms a sliding fit. The specific sliding fit structure will not be described in detail here. The number of brake cylinders 51 can also be two, and the two brake cylinders 51 can pass through the brake beam 623 and the two brake shoe assemblies 61 respectively. interaction.
[0081] In this embodiment, a third sensor (not shown in the figure) may also be included. The third sensor may be arranged on the braking beam 623 for monitoring the thrust of the single beam. The measured braking force is compared to explore the braking force loss caused by the braking beam 623 itself and the sliding friction between the braking beam 623 and the mounting seat 622...
Embodiment 3
[0083] Such as Figure 12 As shown, the difference between the present embodiment and the second embodiment is that the number of the brake cylinder 51 is one, and the brake cylinder 51 is in drive connection with the brake beam 623 through the second brake lever 624 .
[0084] In this embodiment, a fourth sensor may also be included, and the fourth sensor is arranged on the second brake lever 624 for monitoring the thrust of the lever. The brake force loss caused behind the brake lever 624 is convenient for the subsequent improvement of the tread brake device similar to that provided in this embodiment.
PUM
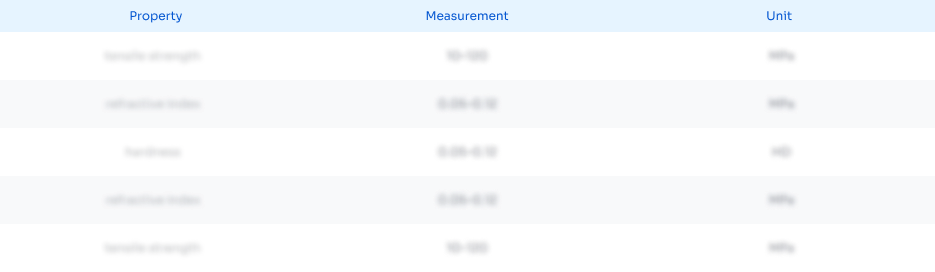
Abstract
Description
Claims
Application Information

- R&D Engineer
- R&D Manager
- IP Professional
- Industry Leading Data Capabilities
- Powerful AI technology
- Patent DNA Extraction
Browse by: Latest US Patents, China's latest patents, Technical Efficacy Thesaurus, Application Domain, Technology Topic, Popular Technical Reports.
© 2024 PatSnap. All rights reserved.Legal|Privacy policy|Modern Slavery Act Transparency Statement|Sitemap|About US| Contact US: help@patsnap.com