Reverse control method of hollow turbine blade wall thickness deviation based on ceramic core positioning compensation
A technology of turbine blades and ceramic cores is applied in the field of reverse regulation of wall thickness deviation of hollow turbine blades based on positioning compensation of ceramic cores, which can solve problems such as excessive wall thickness of hollow turbine blades, improve the qualification rate and service life, and improve matching. relationship, the effect of precise control
- Summary
- Abstract
- Description
- Claims
- Application Information
AI Technical Summary
Problems solved by technology
Method used
Image
Examples
Embodiment Construction
[0050] figure 1 It is the preferred example of the hollow turbine blade of the aero-engine in the present invention, and its length and width are respectively: 138.7mm and 72.9mm.
[0051] In the following, the hollow turbine blade wall thickness deviation reverse regulation method based on ceramic core positioning compensation proposed by the present invention will be described in detail in combination with the example of the hollow turbine blade.
[0052] 1) Obtain the data of the inner and outer contour points of the actual hollow turbine blade
[0053] Use industrial CT to scan the critical section of the actual hollow turbine blade with wall thickness deviation. Among them, the key section is the five sections located at the blade edge curve with the largest curvature value and perpendicular to the direction of the blade stacking axis, such as figure 2 Shown; Afterwards, the inner and outer contour points of the leaf were extracted from the scanned grayscale image, and ...
PUM
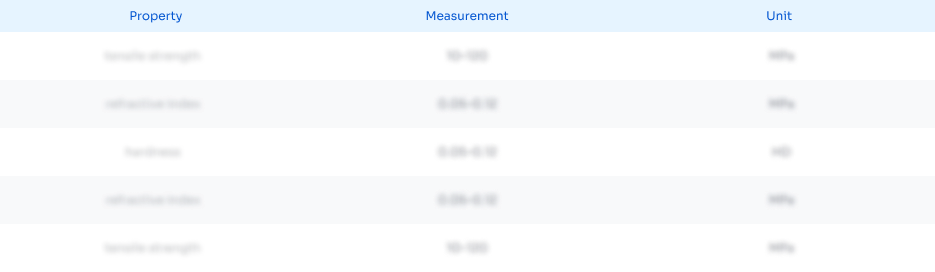
Abstract
Description
Claims
Application Information

- Generate Ideas
- Intellectual Property
- Life Sciences
- Materials
- Tech Scout
- Unparalleled Data Quality
- Higher Quality Content
- 60% Fewer Hallucinations
Browse by: Latest US Patents, China's latest patents, Technical Efficacy Thesaurus, Application Domain, Technology Topic, Popular Technical Reports.
© 2025 PatSnap. All rights reserved.Legal|Privacy policy|Modern Slavery Act Transparency Statement|Sitemap|About US| Contact US: help@patsnap.com