Spatial three-freedom parallel robot mechanism
A degree of freedom and robot technology, applied in the direction of manipulators, manufacturing tools, etc., can solve the problems of low precision, low rigidity, and difficult motion determination of end parts, and achieve the effects of wide application prospects, low motion quality, and high dynamic performance
- Summary
- Abstract
- Description
- Claims
- Application Information
AI Technical Summary
Problems solved by technology
Method used
Image
Examples
Embodiment 1
[0018] Example 1: One of the three-degree-of-freedom spatial parallel robot mechanism
[0019] The overall structure of this embodiment is as figure 1 As shown, the motion table 4 of the mechanism is connected to the frame 1 through three telescopic connecting rods 3, 8, 10, wherein the connecting rods 3, 8 are connected to the motion pair at one end of the motion table 4 by a three-degree-of-freedom spherical hinge 5. 6. The kinematic pairs connected to the frame 1 at the other end are rotating pairs 2 and 9; the kinematic pairs of the connecting rod 10 connecting the motion table 4 and the frame 1 are Hooke hinges 7 and 11, respectively. The movement platform 4 realizes the two-dimensional movement of the plane where the connecting rods 3 and 8 are located and the rotation of the hinges 5 and 6 in a three-degree-of-freedom space movement through the movement of the three telescopic connecting rods 3, 8, 10.
Embodiment 2
[0020] Example 2: Spatial three-degree-of-freedom parallel robot mechanism II
[0021] The overall structure of this embodiment is as figure 2 As shown, the movement table 18 of the mechanism respectively passes through the first and second branches formed by the connecting rods 16, 21, the connecting rods 14, 23, and the third branch and the frame formed by the connecting rod 27 and the connecting rod 25. 12-phase connection. The connecting rods 16, 21 are connected to the sports platform 18 by three-degree-of-freedom ball joints 17, 19 at one end, and the other ends are connected with the connecting rods 14, 23 through the rotating pairs 15, 22; the connecting rod 27 connects the sports platform 18 and the connecting rod. The movement pairs of the frame rod 25 are Hooke hinges 20 and 28, respectively; the connecting frame rods 14, 23, 25 are connected to the frame through the rotating pairs 13, 24, and 26, respectively. The movement table 18 realizes the two-dimensional movement...
PUM
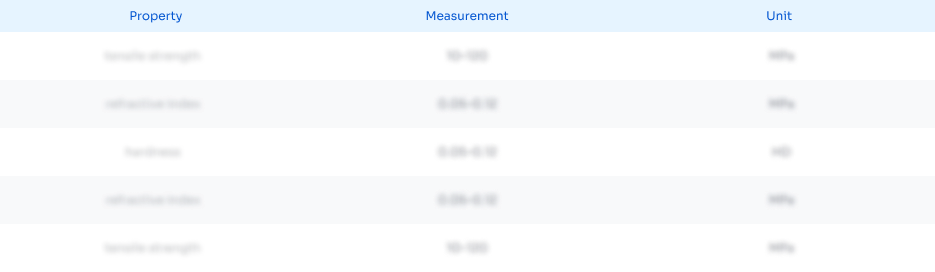
Abstract
Description
Claims
Application Information

- R&D
- Intellectual Property
- Life Sciences
- Materials
- Tech Scout
- Unparalleled Data Quality
- Higher Quality Content
- 60% Fewer Hallucinations
Browse by: Latest US Patents, China's latest patents, Technical Efficacy Thesaurus, Application Domain, Technology Topic, Popular Technical Reports.
© 2025 PatSnap. All rights reserved.Legal|Privacy policy|Modern Slavery Act Transparency Statement|Sitemap|About US| Contact US: help@patsnap.com