Structurally integrated in-situ actuation fully-displaced composite amplified piezoelectric inchworm linear platform
A compound amplification and electric inchworm technology, which is applied to piezoelectric effect/electrostrictive or magnetostrictive motors, electrical components, generators/motors, etc., can solve the problems of reduced platform life, low platform movement speed, and motion stability Reduce and other problems, achieve the effect of reducing the processing and assembly precision requirements, compact platform structure, and improving stability
- Summary
- Abstract
- Description
- Claims
- Application Information
AI Technical Summary
Problems solved by technology
Method used
Image
Examples
Embodiment Construction
[0041] Embodiments of the present invention will be further described in detail below in conjunction with the accompanying drawings.
[0042] Figure 1 to Figure 7 It is a schematic diagram of the structure of the present invention, as shown in the figure, the structurally integrated in-situ drive full-displacement composite amplified piezoelectric inchworm linear platform of the present invention includes a fixed platform 1 and a moving table that is slidably connected by two cross roller guide rails 4 2. There are two retaining bars 2c parallel to the cross roller guide rail 4 under the moving table 2; the first clamping group 12 and the second clamping group 12 arranged along the length direction of the retaining bars 2c are arranged between the two retaining bars 2c. The clamping group 13, the first clamping group 12 and the second clamping group 13 perform telescopic movement along the direction perpendicular to the bar 2c, and their telescopic ends are respectively conne...
PUM
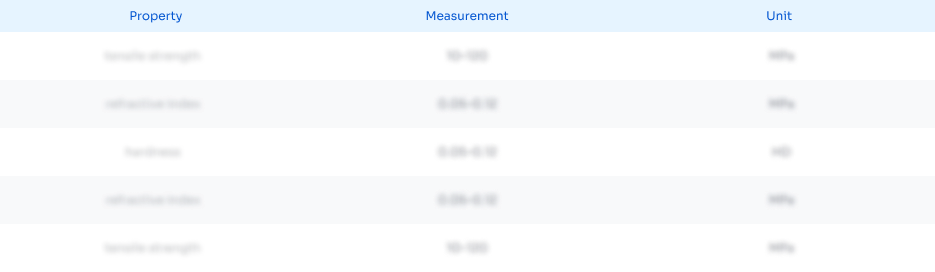
Abstract
Description
Claims
Application Information

- R&D Engineer
- R&D Manager
- IP Professional
- Industry Leading Data Capabilities
- Powerful AI technology
- Patent DNA Extraction
Browse by: Latest US Patents, China's latest patents, Technical Efficacy Thesaurus, Application Domain, Technology Topic, Popular Technical Reports.
© 2024 PatSnap. All rights reserved.Legal|Privacy policy|Modern Slavery Act Transparency Statement|Sitemap|About US| Contact US: help@patsnap.com