Manufacturing method of backlight source transflective film layer, backlight source and UV ink printer
A production method and backlight technology, applied in the field of microdisplay, can solve the problems of uneven light mixing, uneven light mixing on the front of surface light sources, affecting market competitiveness, etc., to achieve uniform light distribution and improve product yield.
- Summary
- Abstract
- Description
- Claims
- Application Information
AI Technical Summary
Problems solved by technology
Method used
Image
Examples
Embodiment Construction
[0033] The following will clearly and completely describe the technical solutions in the embodiments of the present invention with reference to the accompanying drawings in the embodiments of the present invention. Obviously, the described embodiments are only some, not all, embodiments of the present invention. Based on the embodiments of the present invention, all other embodiments obtained by persons of ordinary skill in the art without making creative efforts belong to the protection scope of the present invention.
[0034] Please refer to figure 1 , the invention provides a method for manufacturing a backlight transflective film layer, comprising:
[0035] S101: Provide a light board assembly 100, the light board assembly 100 includes a plurality of chips 150;
[0036] S102: Align the UV ink printer with the lamp panel assembly 100, move the UV ink printer to print the chip 150 to form the UV ink layer 140, and the UV ink layer 140 corresponds to the chip 150 one by one;...
PUM
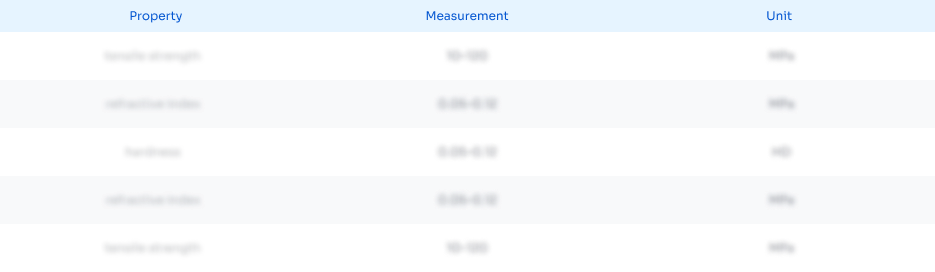
Abstract
Description
Claims
Application Information

- R&D
- Intellectual Property
- Life Sciences
- Materials
- Tech Scout
- Unparalleled Data Quality
- Higher Quality Content
- 60% Fewer Hallucinations
Browse by: Latest US Patents, China's latest patents, Technical Efficacy Thesaurus, Application Domain, Technology Topic, Popular Technical Reports.
© 2025 PatSnap. All rights reserved.Legal|Privacy policy|Modern Slavery Act Transparency Statement|Sitemap|About US| Contact US: help@patsnap.com