High-expansion-rate water-blocking yarn and production process thereof
A production process, water-blocking yarn technology, applied in yarn, liquid/gas/steam fiber/sliver/roving treatment, liquid/gas/steam removal, etc. Water yarn has a lot of glue on it, etc., to achieve the effect of good water absorption
- Summary
- Abstract
- Description
- Claims
- Application Information
AI Technical Summary
Problems solved by technology
Method used
Image
Examples
Embodiment 1
[0033] A production process of high expansion rate water-blocking yarn, the steps are as follows:
[0034] A Preparation of aramid water-blocking yarn: impregnate the unrolled 1500D aramid fiber into the binder solution, and pass the impregnated fiber through double rollers to remove excess binder solution;
[0035] B. Process the fiber obtained in step A through a heat channel, the temperature of the heat channel is 120°C, and the heat treatment time is 1 min;
[0036] C impregnating the fibers obtained in step B with water-soluble resin glue and removing excess glue through double rollers;
[0037] D. Process the fiber obtained in step C through a heat channel to cross-link the water-soluble resin glue into a superabsorbent resin. The temperature of the heat channel is 195°C, and the heat treatment time is 1.5 minutes;
[0038] E, rewinding the fiber obtained in step D to obtain aramid water-blocking yarn with high expansion rate;
[0039] Among them, the adhesive solution...
Embodiment 2
[0041] The difference between this embodiment and embodiment 1 is:
[0042] Adhesive solution is to mix and stir 5 parts of polyvinyl alcohol, 0.25 parts of glutaraldehyde, and 95 parts of deionized water evenly; water-soluble resin glue is made of sodium polyacrylate post-crosslinking water-absorbing resin solution 50 parts, polyethylene glycol 2 parts were mixed with 48 parts of deionized water and stirred evenly.
Embodiment 3
[0044] A production process of high expansion rate water-blocking yarn, the steps are as follows:
[0045] A Preparation of aramid water-blocking yarn: impregnate the unrolled 1500D aramid fiber into the binder solution, and pass the impregnated fiber through double rollers to remove excess binder solution;
[0046]B. Process the fiber obtained in step A through a heat channel, the temperature of the heat channel is 125° C., and the heat treatment time is 2 minutes;
[0047] C impregnating the fibers obtained in step B with water-soluble resin glue and removing excess glue through double rollers;
[0048] D. Process the fiber obtained in step C through a heat channel to cross-link the water-soluble resin glue into a superabsorbent resin. The temperature of the heat channel is 200°C, and the heat treatment time is 0.5 min;
[0049] E, rewinding the fiber obtained in step D to obtain aramid water-blocking yarn with high expansion rate;
[0050] Among them, the adhesive solutio...
PUM
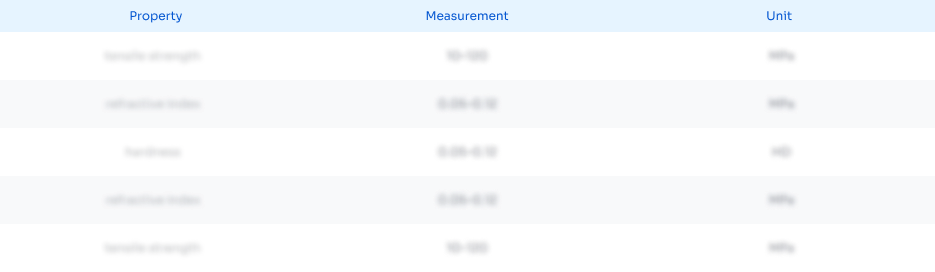
Abstract
Description
Claims
Application Information

- R&D Engineer
- R&D Manager
- IP Professional
- Industry Leading Data Capabilities
- Powerful AI technology
- Patent DNA Extraction
Browse by: Latest US Patents, China's latest patents, Technical Efficacy Thesaurus, Application Domain, Technology Topic, Popular Technical Reports.
© 2024 PatSnap. All rights reserved.Legal|Privacy policy|Modern Slavery Act Transparency Statement|Sitemap|About US| Contact US: help@patsnap.com