Micro-positioning platform based on piezoelectric ceramic driving and modeling and control method thereof
A piezoelectric ceramic drive, micro-positioning platform technology, applied in general control systems, control/regulation systems, simulators, etc., can solve the problems of increasing control signal oscillation, not considering inverse compensation errors and modeling errors, etc., to achieve Stable control, guaranteed modeling accuracy, and high identification accuracy
- Summary
- Abstract
- Description
- Claims
- Application Information
AI Technical Summary
Problems solved by technology
Method used
Image
Examples
Embodiment 1
[0072] In this embodiment, a micro-positioning platform based on piezoelectric ceramic drive is provided. For details, please refer to image 3 , is the structural block diagram of the micro-positioning platform, including:
[0073] Hardware part: industrial computer 1, and it is provided with controller inside; Piezoelectric ceramic drive power supply 2, and it is connected with displacement sensor; Data acquisition card 3 and precision positioning table 4;
[0074] Software part: the Simulink software loaded in the industrial computer, and based on the software part, the communication connection between the industrial computer 1 and the data acquisition card 3 is realized to form a closed-loop deviation control.
[0075] Specifically, in this embodiment, based on the structural form of the micro-positioning platform disclosed above, the working principle of the micro-positioning platform is as follows: the controller of the industrial computer 1 is customized based on the Si...
Embodiment 2
[0077] This embodiment provides a kind of modeling method based on the micro-positioning platform driven by piezoelectric ceramics, and its micro-positioning platform is the micro-positioning platform in the above-mentioned embodiment one, and the modeling method adopts the Hammerstein model such as Figure 4 As shown, as the modeling basis, and includes the following modeling steps:
[0078] S1. Construct a static nonlinear function based on the Bouc-Wen model, and adopt the particle swarm algorithm to identify its unknown parameters in the model; the mathematical expression of the Bouc-Wen model is:
[0079]
[0080] Among them, u is the driving voltage of the control signal, v is the output displacement signal, h is the hysteresis item of the model, d is the gain, α is the amplitude of the control hysteresis loop, β, γ control the shape of the hysteresis loop; and d, α, Both β and γ are unknown parameters in the Bouc-Wen model; specifically, in the above expression, ther...
Embodiment 3
[0117] This embodiment provides a control method for a micro-positioning platform driven by piezoelectric ceramics. The micro-positioning platform is the micro-positioning platform in the first embodiment above. The control method adopts a composite control method of feedforward control and feedback control, and Including the following control steps:
[0118] S1. Feedforward control: based on the inverse Bouc-Wen model to compensate the static hysteresis of the micro-positioning platform;
[0119] S2. Feedback control: based on H ∞ The controller suppresses model uncertainty and external disturbances.
[0120] Specifically, the compound control block diagram formed by the control method provided in this embodiment can be referred to Figure 10 shown, where x d is the reference input, N -1 is the inverse Bouc-Wen model, k is the constant gain, N is the Bouc-Wen model, G(s) is the linear dynamic model, K(s) is H ∞ controller.
[0121] As mentioned above, the inverse Bouc-...
PUM
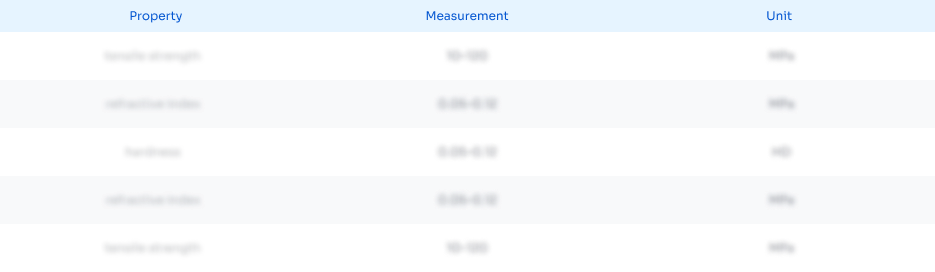
Abstract
Description
Claims
Application Information

- R&D
- Intellectual Property
- Life Sciences
- Materials
- Tech Scout
- Unparalleled Data Quality
- Higher Quality Content
- 60% Fewer Hallucinations
Browse by: Latest US Patents, China's latest patents, Technical Efficacy Thesaurus, Application Domain, Technology Topic, Popular Technical Reports.
© 2025 PatSnap. All rights reserved.Legal|Privacy policy|Modern Slavery Act Transparency Statement|Sitemap|About US| Contact US: help@patsnap.com