Early-strength waterproof foaming agent for foam concrete
A foam concrete and foaming agent technology, which is applied in the field of early-strength waterproof foam concrete foaming agent, can solve the problems of poor stability of foam concrete slurry, affecting the popularization and use of foam concrete, and one-time pouring height difference, etc. One-time pouring height, fine and uniform foam, and the effect of reducing mold collapse
- Summary
- Abstract
- Description
- Claims
- Application Information
AI Technical Summary
Problems solved by technology
Method used
Image
Examples
Embodiment 1
[0020] Weigh 100 parts of water; 9.5 parts of potassium lauryl ether phosphate, 8 parts of lauryl amidopropyl hydroxysultaine, 5 parts of cocoic acid diethanolamide; 1.2 parts of gum arabic, 1.5 parts of pentasodium triphosphate, ammonium chloride 0.9 parts; 1.6 parts of sodium sulfate, 2.5 parts of sodium carbonate; 1.8 parts of sodium methyl silicate, mix all components evenly to get foaming agent. Refer to JG / T266-2011 "Foamed Concrete" for foaming agent performance test. The foaming agent prepared in this example was prepared into A05 grade foam concrete, and the 3d strength, 28d strength and water absorption performance tests were performed. The test results are shown in Table 1.
Embodiment 2
[0022] Weigh 100 parts of water; 12 parts of potassium lauryl ether phosphate, 5 parts of lauryl amidopropyl hydroxysultaine, 4.5 parts of cocoic acid diethanolamide; 1.9 parts of gum arabic, 1 part of pentasodium triphosphate, ammonium chloride 0.6 parts; 2.5 parts of sodium sulfate, 2 parts of sodium carbonate; 2 parts of sodium methyl silicate, mix all components evenly to get foaming agent. Refer to JG / T266-2011 "Foamed Concrete" for foaming agent performance test. The foaming agent prepared in this example was prepared into A05 grade foam concrete, and the 3d strength, 28d strength and water absorption performance tests were performed. The test results are shown in Table 1.
Embodiment 3
[0024] Weigh 100 parts of water; 14 parts of potassium lauryl ether phosphate, 6 parts of lauryl amidopropyl hydroxysultaine, 4 parts of cocoic acid diethanolamide; 1.5 parts of gum arabic, 1.8 parts of pentasodium triphosphate, ammonium chloride 1 part; 1.6 parts of sodium sulfate, 2.2 parts of sodium carbonate; 1.4 parts of sodium methyl silicate, and prepare by uniformly mixing all components to obtain a foaming agent. Refer to JG / T266-2011 "Foamed Concrete" for foaming agent performance test. The foaming agent prepared in this example was prepared into A05 grade foam concrete, and the 3d strength, 28d strength and water absorption performance tests were performed. The test results are shown in Table 1.
PUM
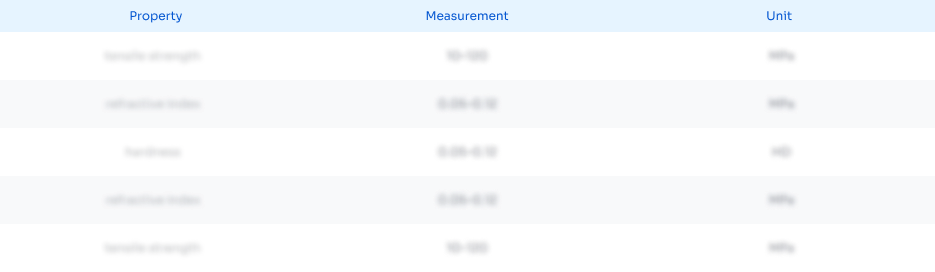
Abstract
Description
Claims
Application Information

- R&D
- Intellectual Property
- Life Sciences
- Materials
- Tech Scout
- Unparalleled Data Quality
- Higher Quality Content
- 60% Fewer Hallucinations
Browse by: Latest US Patents, China's latest patents, Technical Efficacy Thesaurus, Application Domain, Technology Topic, Popular Technical Reports.
© 2025 PatSnap. All rights reserved.Legal|Privacy policy|Modern Slavery Act Transparency Statement|Sitemap|About US| Contact US: help@patsnap.com