Method for forming fan-shape polygon frame forge piece
A multi-frame, fan-shaped technology, applied to engine components, mechanical equipment, etc., can solve problems such as inapplicability
- Summary
- Abstract
- Description
- Claims
- Application Information
AI Technical Summary
Problems solved by technology
Method used
Image
Examples
Embodiment 1
[0015] An installation side of GEPS company is figure 1 , figure 2 As shown, its external dimensions A and B are about 532mm and 223mm, and its material is NIMONIC263 heat-resistant alloy determined by the American special standard AMS5886A. Rough, punching, upsetting height control 42mm ~ 45mm, punching control heating temperature 1130 ℃ ± 10 ℃, punch preheating 200 ℃ ~ 300 ℃. see reaming image 3 , At this time, the billet heating temperature is 1130°C±10°C, the mold is preheated at 150°C-300°C, pay attention to controlling the inner diameter to about Φ300mm, and the wall thickness and height of the reaming ring are 41mm±1.5mm and 45mm±2mm. Marking marks on the end face of the reaming ring refer to Figure 4 , for the corner position of this embodiment, take the mark according to the angle ratio and connect it with the center of the reaming ring respectively to form α 1 、α 2 , β 1 , β 2 Four corners, take β 1 = β 2 , α 2 >α 1 . To lengthen marked reaming rings o...
Embodiment 2
[0017] The crank arm of a switch factory is Figure 8 As shown, the material is 40CrNiMo, and the three sides of the outer dimension are about 265mm. The processing procedure is as follows: select the bar material, cut the material according to the required blank weight, upsetting, punching, and the height is controlled at 40mm. Heat at 200°C to 300°C, and heat the blank at 1130°C±20°C. At this time, the wall thickness and height of the reaming ring are 35mm±1.5mm and 40mm±2mm. The corner position of this embodiment is almost an equilateral triangle, and the corner position can be Mark by three equal angles, or mark by three equal sides, that is, by the proportion of the line segment, and stretch the marked reaming ring on one side. At this time, the heating temperature is the same as above, and the preheating is the same as above. Pay attention to ensure that the mark is within a certain range. The blanks inside cannot be reduced to ensure that the subsequent process needs to...
PUM
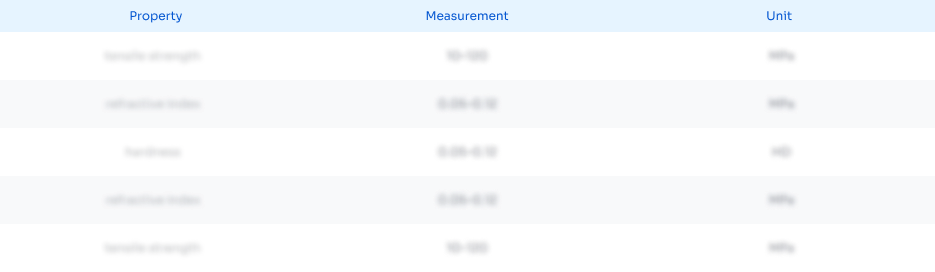
Abstract
Description
Claims
Application Information

- R&D
- Intellectual Property
- Life Sciences
- Materials
- Tech Scout
- Unparalleled Data Quality
- Higher Quality Content
- 60% Fewer Hallucinations
Browse by: Latest US Patents, China's latest patents, Technical Efficacy Thesaurus, Application Domain, Technology Topic, Popular Technical Reports.
© 2025 PatSnap. All rights reserved.Legal|Privacy policy|Modern Slavery Act Transparency Statement|Sitemap|About US| Contact US: help@patsnap.com